ウエハプロセス評価装置&超微細加工評価装置
はじめに
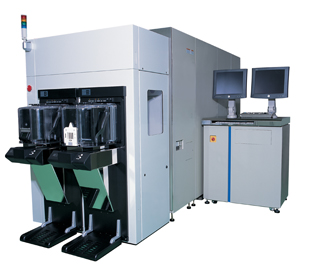
半導体技術の進歩はめざましく、素子の微細化、高集積化が加速しており、そして半導体製造における歩留まり管理がますます重要になってきています。このような環境において、ウエハ上の欠陥の存在は微細加工や量産に対して大きな悪影響を及ぼします。このため品質管理は厳重に行なわれ、ウエハの欠陥検査工程は極めて重要になっています。
欠陥検査方式
ウエハの欠陥検査装置には光学方式と走査電子顕微鏡(SEM)方式とがあります。
光学方式の特長は、高速で微小な異物や欠陥を検出することで、欠陥の大きさ種類によっては色情報を含めた有用な情報を得られます。又、SEM方式では得られない、ある程度下層にある欠陥の検出や観察が可能です。ただし、光学方式は、分解能が光の波長に原理的に制約される為、可視光であれば、0.2μm程度の欠陥を検出することが限界です。
これに比べてSEM方式では、光学方式に比較して、原理的に分解能で有利な為、光学方式で検出されたウエハ表層の微小欠陥、パーティクルの形状や成分をより詳しく観察したり、分析する事が可能となります。半導体の細線化が進むにともない、歩留まり管理で問題となる欠陥サイズもサブミクロンとなり、光学方式とSEM方式を組み合わせて運用する事が不可欠となっています。
特にSEM方式で得られる情報は、欠陥の起源や原因を突き止め、プロセスの改善を行う為に利用されています。それは、電子線を用いたSEM方式の特長として、形状や材質に伴うコントラストの変化による、残膜や微小形状欠陥の検出だけではなく、電気的変化を伴う変化から、電気的不良などの致命的欠陥を検出できる可能性を持っているからです。
ただし、一般にSEMは高い分解能をもっていますが、広い面積の中から微小な異物や欠陥を探し出すことは不得手です。一方、光学方式は広い面積の中から、微小な欠陥や異物を高速で探し出すことが出来ます。
現在、光学方式で欠陥や異物を見つけ、次にSEM方式で高分解能観察するという方法で、光学方式とSEM方式を組み合わせて運用する事が一般的で、SEM方式は光学方式とステージ座標の共有化を行う為に、ネットワーク接続されています。その結果、光学方式で検出された欠陥や異物などのステージ座標データを、ネットワークを通じて受け取ることで、SEM方式は容易に微小な欠陥や異物を探し出すことが出来るようになっています。
装置の特徴
ウエハプロセス評価装置の特長は、光学方式では判断が困難な微小異物・欠陥の検査を行うことが出来ることです。また、自動欠陥検出(Auto Defect Review: ADR)/自動欠陥分類(Auto Defect Classification: ADC)システムを付加することで、欠陥の自動検出や、自動分類が出来ます。自動検出した欠陥を各プロセスやレイヤ毎に分類する事で、欠陥の原因を突き止め、プロセス改善に利用されます。更に、本装置ではウエハを水平だけでなく、傾斜、回転して観察することができ、それによって欠陥を特長づけるより多くの情報を得る事ができます。 図1 a,b は異物の観察例で、水平と傾斜、回転をして観察した場合の見え方の違いを示したものです。 水平での観察例では、異物が表面に付着しているのか、パターンの側面や下に埋もれているかを判断するのは困難ですが、傾斜、回転をした方ではそれを的確に判断することができ、さらに水平の状態に比べ、より緻密に欠陥部の形態観察ができることが分かります。このように、ウエハの傾斜・回転観察は、水平観察に比較し、より多くの情報を得る事ができます。
異物の観察例
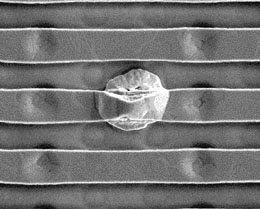
図1a ステ-ジ水平での像
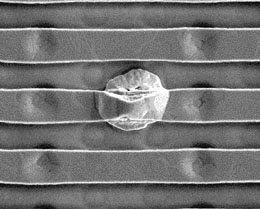
図1b ステージ傾斜回転での像
外観検査による欠陥の解析
半導体で問題となる欠陥の種類には色々なタイプがあります。表面に付着した異物、パターンの形状の異常、前工程での欠陥が原因となって発生するパターン異常(パターンの下に異物が埋もれる)などです。欠陥の原因追及には、検出された欠陥がどのタイプなのかを分類する必要があります。このためウエハプロセス評価装置は自動欠陥検出(Auto Defect Review: ADR)/自動欠陥分類(Auto Defect Classification: ADC)の機能が付加されたシステムとなっています。 本システムでは直径300mm(又は200mm)サイズのウエハに対応して、光学式欠陥検査装置から得られた座標データに基づいてステージが欠陥点に移動します。しかし、光学式欠陥検査装置から得られる位置精度はウエハプロセス評価装置に対して誤差を含み、また、欠陥のサイズは1μm以下になる物もあります。ADRは光学式欠陥検査装置からもらった座標データに基づき、そのような微小な欠陥を視野の中から自動的に検出して、適正倍率で画面中央 に表示させる機能を持ちます。欠陥検出には Arrayモードと Die to Die モードとの2つがあります。Arrayモードは基準となる画像を記録しておき、基準画像と欠陥点を含む画像との比較を行い欠陥点を検出するモードで、 Die to Dieモードは欠陥点と同じ座標に相当する隣のチップの画像を基準とし、欠陥点を含む画像との比較を行い欠陥点を検出するモードです。このため、Arrayモードはメモリーセルのような繰り返しパターンでの欠陥検出に有効で、Die to Dieモードよりも高スループットです。一方 Die to Dieモードは、ロジック部のパターンのような検査点毎に基準画像を取る必要が有るといった、いわゆる繰り返しがないパターンでの欠陥検出に有効です。 図2bはADRよって得られた結果の一例です。
自動欠陥検出(ADR)自動欠陥分類(ADC)の出力例
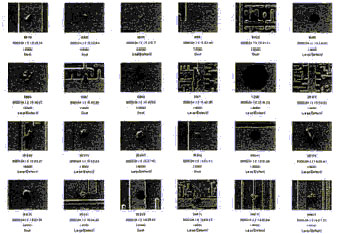
図2a 自動欠陥検出(ADR)出力例
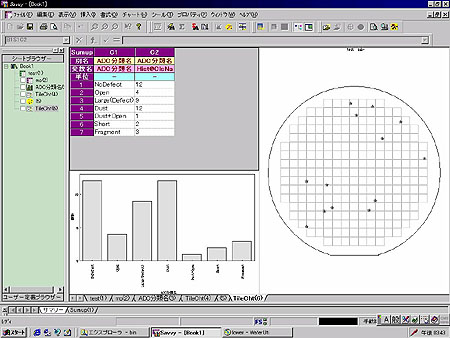
図2b 自動欠陥分類(ADC)出力例
このように送られてきた座標データに基づいてステージが欠陥点に移動し、その位置での画像の中から自動的に欠陥画像を収録するのがADRです。さらにADCではADRで得られた画像から、その大きさや種類に分けて欠陥を分類します。
図2a,bは自動欠陥検出(ADR)及び自動欠陥分類(ADC)の出力例を示したもので、図2aはADRよって得られた結果の一例です。また、図2bはADCの出力例で、ユーザがあらかじめ分類項目を指定しておくことで、その項目に従ってADRの結果から図2bに示したようなヒストグラムを得ることが出来ます。その結果を解析することで、欠陥の発生プロセスや原因を把握し、その対応策を講じて歩留まり向上が計られます。さらに得られた結果をネットワークを通して歩留まり管理システム(Yield Management System :YMS)に送ることで、歩留まり向上の判断材料としての集中管理(データベース化等)が行えます。
このシステムでは、あらかじめレシピ作成で条件を設定することで、無人でのウエハの自動交換、自動欠陥検査が可能です。無人による自動運転は、作業効率の向上が計れ、オペレータによる人為的ミスを極力少なくすることができ、信頼性の高いデータを得ることが出来ます。その結果、より正確な欠陥の発生プロセスや原因の把握が可能となり、歩留まり向上に大きく貢献することが出来ます。