日本電子工業株式会社様
~高周波焼入れ技術の進化を支える金属3Dプリンター
日本電子工業株式会社は、高周波焼入れ技術の分野で長年の実績を持ち、金属積層造形技術を採用することでさらなる進化を目指しています。今回のインタビューでは、日本電子工業が金属3Dプリンターを導入した経緯や今後の展望、日本電子に寄せる期待について詳しくお話を伺いました。
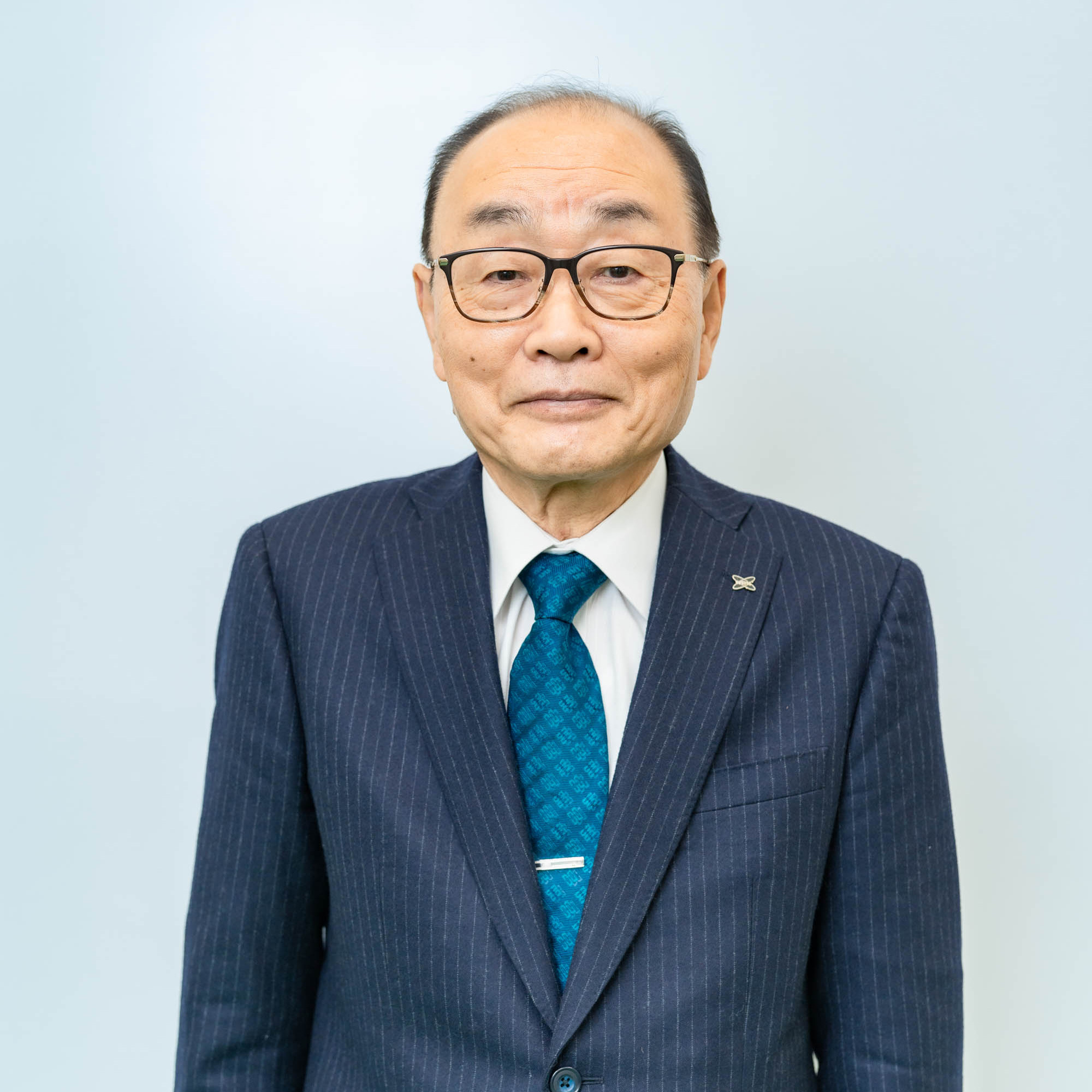
竹内 博次 (たけうち ひろつぐ)
日本電子工業株式会社 代表取締役社長
関西大学工学部金属工学科を卒業後、1977年に日本電子工業株式会社へ入社。装置製造部門で技術開発を担当し、プラズマ(イオン)窒化技術の開発に従事。その後、さらなる専門性を高めるため、茨城大学大学院理工学研究科博士後期課程物質科学専攻に進学し工学博士号を取得。大学院在学中は、茨城大学の教授から指導を受けながら、仕事と学業を両立させた。49歳で取締役に就任し、その後11年間子会社社長を務めた。58歳で日本電子工業株式会社の代表取締役社長に就任。現在に至る。
内製化実現に向けて金属3DプリンターJAM-5200EBMを導入
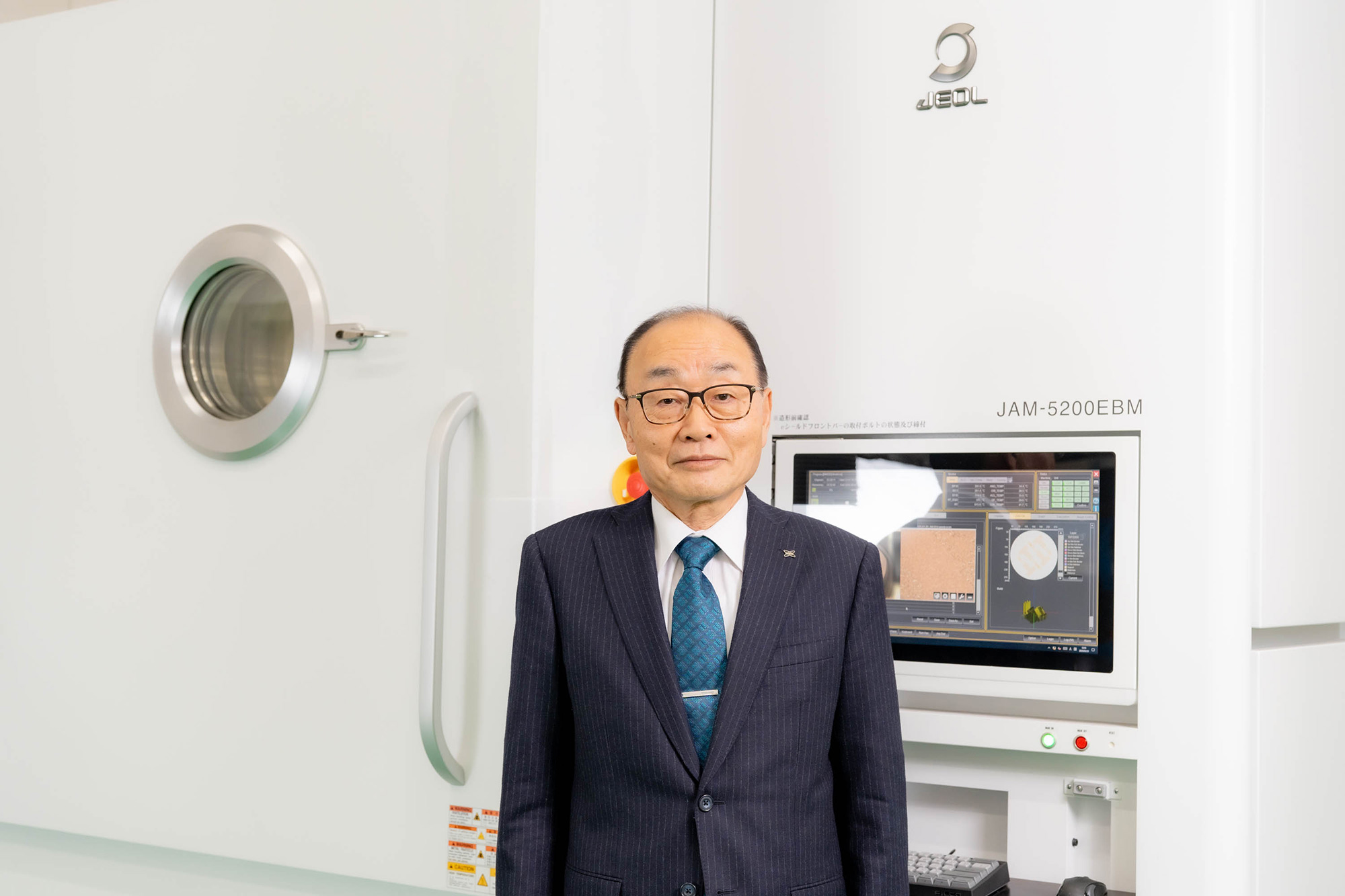
――金属3Dプリンターを導入した経緯を教えてください。
弊社は鉄鋼材料の高周波焼入れ受託加工および装置の製造販売を長年手掛けております。高周波焼き入れに欠かせないのが、銅製の加熱コイルです。このコイルはこれまで協力会社で切断や曲げ、穴開け、ロウ付けといった加工を行い製作していましたが、協力会社ですと技術的にこちらが思うようなものができないこともありました。また、加熱コイルは高周波焼き入れにおいて必要不可欠な部品であり、将来的に受託加工を安定して受注するには内製化も必要と考えていました。
こうした背景から金属3Dプリンターの導入検討を始めました。金属3Dプリンターの導入によるコイルの複雑形状の実現と内製化による安定供給が、顧客満足度向上や受注の拡大に繋がると考えました。また、装置販売時に付属品として提供することで、安定した受注も期待されます。
――電子ビーム方式の金属3Dプリンターを選ばれた理由を教えてください。
弊社が作る銅製の加熱コイルは銅合金ではなく純銅にこだわっています。材料コストでは純銅の方が高くなりますが、最終的な電力コストまで考えると電気伝導率の高い純銅の方が良いと判断しています。
金属3Dプリンターは電子ビーム方式とレーザー方式の選択肢がある中で、純銅の造形にはエネルギー変換効率の高い電子ビーム方式が優位であるということでこちらを選びました。銅合金であればレーザー方式でも良かったのですが、純銅の場合は電子ビーム方式の方が良いと考えました。
――他社製品ではなく、日本電子製を選んだ理由は何ですか?
国内ではレーザー方式の金属3Dプリンターは何社かありましたが、電子ビーム方式は日本電子さんが唯一取り扱っているということでご相談させていただきました。
また、日本電子さんは弊社と長年の歴史的な繋がりがあり、重要な株主でもあります。さらに、電子顕微鏡をはじめとする精密分析機器や産業用機器を製造する世界のトップメーカーとして、全幅の信頼を寄せているという点も日本電子さんを選んだ理由になります。
――導入によって、自社の製造プロセスにどのような変化がありましたか?
大きな変化はまだありませんが、将来的に加熱コイルの品質向上や短納期化を目指しています。これまで協力会社で試作品の製作に2~3週間かかっていたものが、内製化により2~3日で対応可能になり、顧客からも高評価を得ています。
設備の操作性は非常に高く、ユーザー目線に立った設計がされていると感じています。一方で、銅粉末の除去や高温化した銅の冷却工程には改善の余地があり、さらなる効率化を模索していければと思います。
AI搭載など、今後も更なる進化を期待
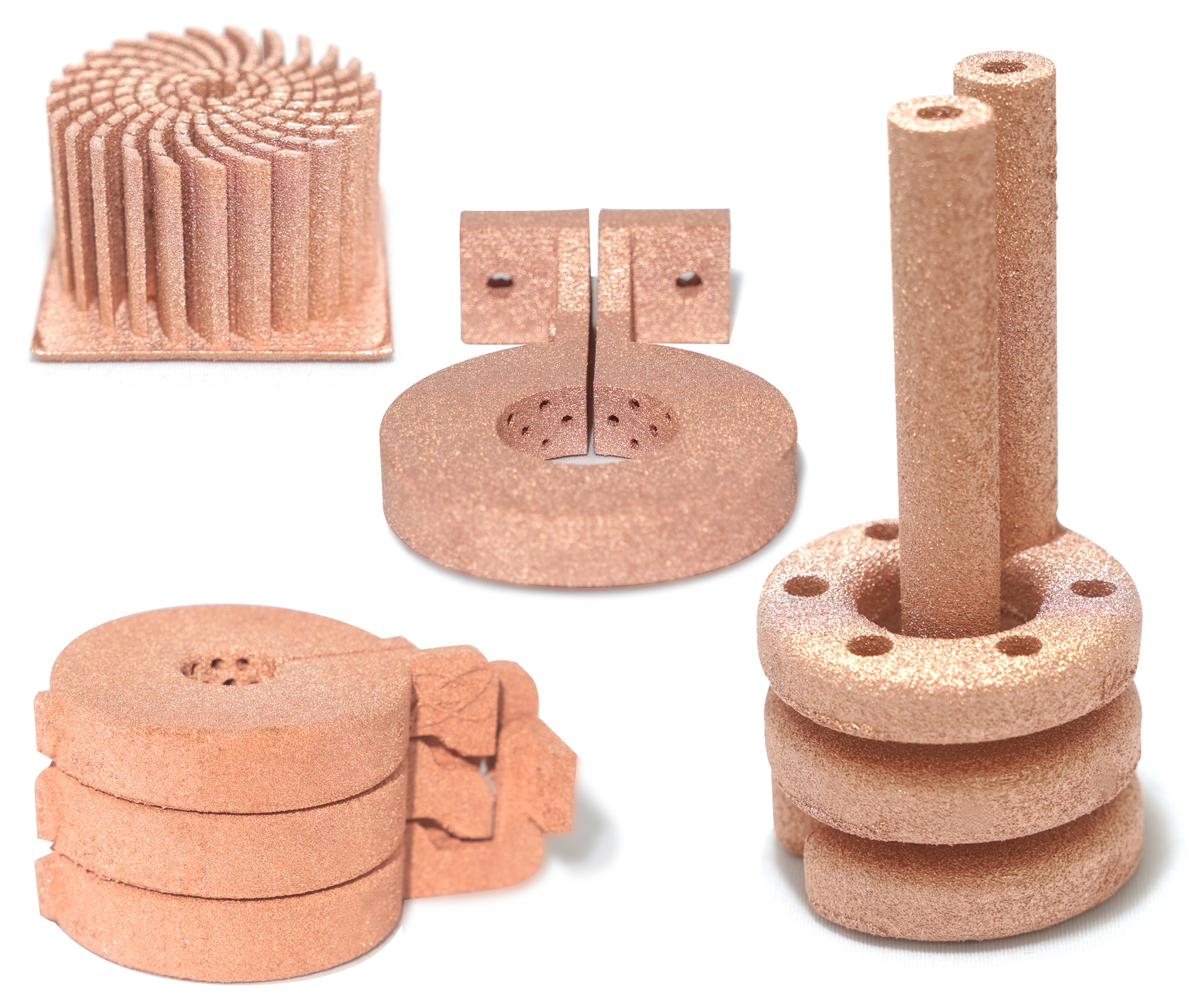
――導入後のコスト削減や生産性向上について、どのような成果が出ていますか?
まだ稼働開始から間もないため、試作品の製作を中心に運用しています。コスト削減や生産性向上については今後の課題ですが、銅粉末処理コストの削減に向けて日本電子さんの担当者と相談を進めています。
――「JAM-5200EBM」を活用した新規事業の計画などはありますか?
現在は社内での加熱コイル製作を主体としていますが、バルブや電気部品、焼き入れ加工用の鉄素材など、多岐にわたる試作品の引き合いを受けています。特に銅の電気伝導率や熱伝導性を活かした部品開発に力を入れており、これらを新たな事業展開に繋げたいと考えています。
―― 日本電子の製品に対して、さらに期待する点はありますか?
弊社は鉄鋼材料の高周波焼入れやプラズマ窒化、PVD、DLCなど表面改質技術を主力事業としています。一方で、弊社はまだ積層造形技術の経験が浅いため、日本電子さんの指導を受けつつ、事業を進めてまいりたいと考えています。
また、昨今は「AI」が声高に叫ばれておりますので、産業機械のなかにも取り入れて頂ければと思います。 例えば、データをインプットして条件設定をすると自動で製造できるような機能があると、より使いやすくなるのではないでしょうか。
造形物表面の滑らかさに課題
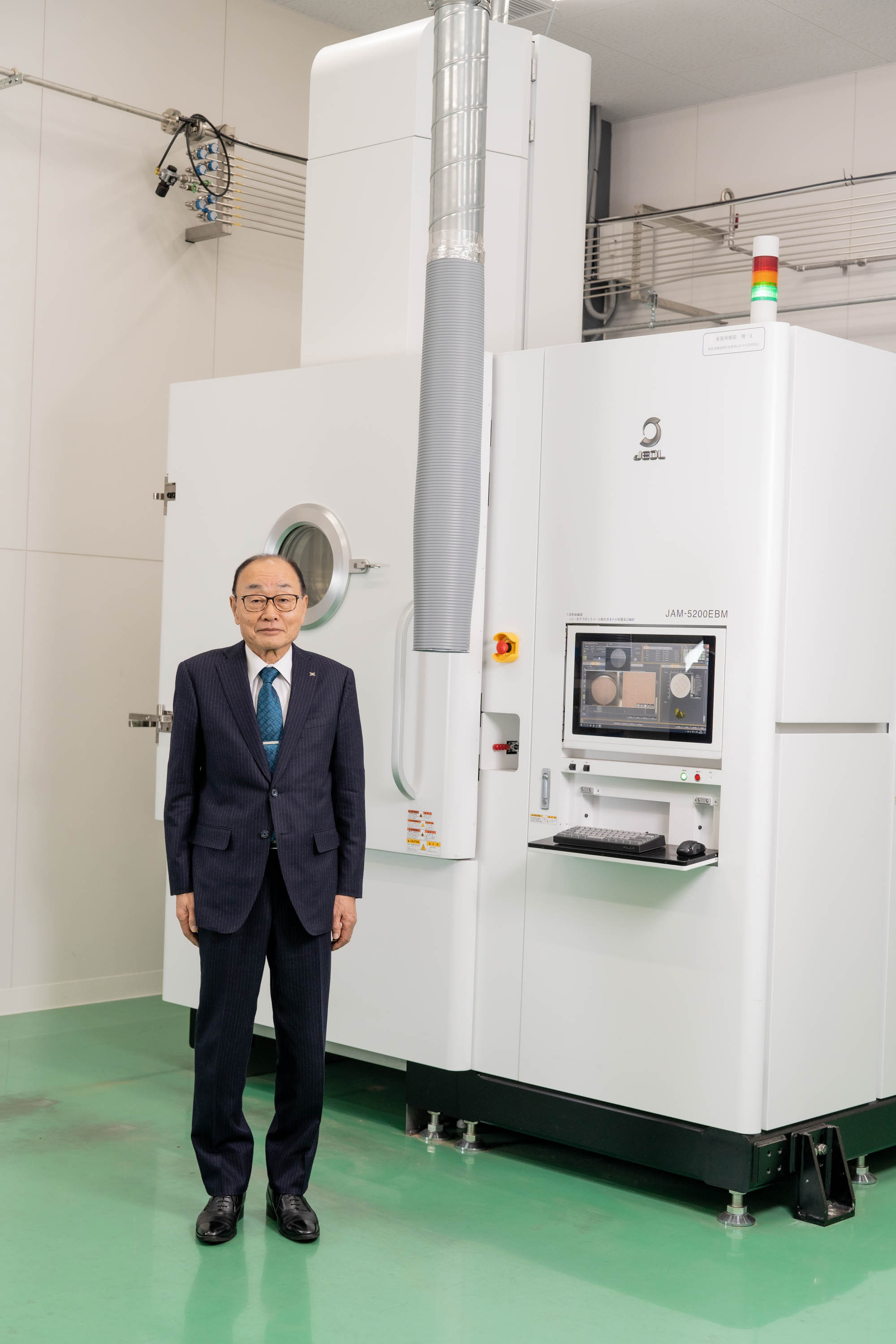
――導入にあたって、難しかった点や課題があれば教えてください。
造形品内部に残る金属粉末の除去や表面の粗さの改善が課題です。現状でも機能的に問題はありませんが、表面を滑らかに仕上げることで、より商品価値が高まると考えています。
――現場での操作性やメンテナンスのしやすさについて、どのように評価していますか?
非常に操作しやすく、メンテナンスも容易です。現場作業者の負担が少なく、使いやすい設備だと感じています。
―― 導入後のトラブル対応やサポート体制についての印象を教えてください。
トラブル時には迅速な対応をいただいており、営業・技術・サービスの連携が素晴らしいです。サポート体制の充実が高い安心感に繋がっています。
例えば、電子ビーム溶接機はドイツのものを導入しましたが、サービスに関しては時差があるため問い合わせ対応に3~4日かかることがあります。また、言語も英語やドイツ語なので翻訳が必要です。文化的にも、海外とのやり取りは回答がはっきりしており、できないものはできない、と明確な回答が返ってきます。一方で、 日本電子さんの担当者に相談した場合には、営業・技術・サービスが一丸となってサポートしてくれるため、安心して利用することができます。
――現場からのフィードバックを受けて、良い点や改善が必要だと感じる点はありますか?
導入から間もないため、現場の習熟度には課題が残ります。今後、運用が進む中で気付いた点を日本電子さんと共有し、改善を図ってまいりたいと考えています。
―― 実際にご活用いただいた上で、どんな企業や団体にこの製品が向いているとお考えでしょうか?
弊社としては初めての取り組みであり、なかなか難しい質問ですが、自動車部品などのものづくり産業の開発部門や工業技術センターなどでの研究に適していると考えます。また、アルミや銅、チタンなどを使用した部品の開発や、半導体関連部品の製造にも活用できる可能性があります。 中小企業が直接導入することは難しいかもしれませんが、県の工業センターなどの公共施設に導入されることで、多くの中小企業が利用する機会が生まれると思います。また、展示会でも予想外の分野からの引き合いがあり、幅広い産業分野に応用できる可能性があると感じています。
―― 「JAM-5200EBM」の現場における更なる活用について、今後の展望などございましたらお聞かせください。
現在は社内で使用する高周波加熱用コイルの製作を中心に進めていますが、将来的には高周波焼入れ装置の販売先へのPRや、付加価値の高い新製品の開発へ展開してまいりたいと考えています。また、全方位型の事業展開を目指し、さらなる技術力の向上に努めてまいります。