金属3Dプリンターの基礎知識:各方式の違いと特徴を徹底解説
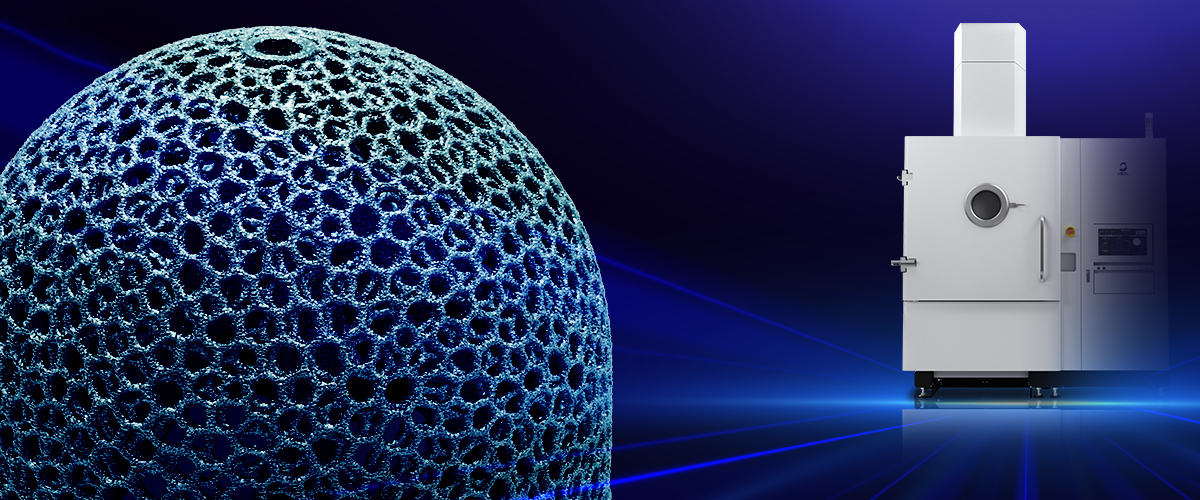
金属3Dプリンターは従来の金属加工法と比べて複雑形状を製作することができ、その他にも材料ロスの削減、工期の短縮などさまざまなメリットがあり、実用化が広がっています。本コラムでは、金属3Dプリンターの基本的な仕組みと主要な造形方式について詳しく解説します。
金属3Dプリンター(積層造形装置)とは?
金属3Dプリンターとは、3次元CADデータをもとに、金属粉末や金属ワイヤーを材料として、レーザーや電子ビームなどで溶融させ、一層ずつ積層しながら立体形状を造形する装置です。金属材料の加工法は、切削、鋳造、鍛造、板金加工、プレス加工、粉末冶金、接合などが挙げられますが、金属3Dプリンターは新たな工作機械と呼ぶ事ができます。
金属3Dプリンターの歴史
金属3Dプリンターの開発は、1980年代に遡ります。1987年にアメリカのチャック・ハル氏が、光造形法を用いた初の商用3Dプリンター「SLA-1」を開発しました。これは樹脂を材料としていましたが、その後、金属粉末をレーザーで溶融させる技術が開発され、1990年代には商用の金属3Dプリンターが登場しました。2013年のアメリカのオバマ大統領(当時)の一般教書演説以後、金属3Dプリンターが世界中で注目されるようになり、開発プロジェクトがアメリカ、ヨーロッパ、中国などで開始されました。日本においても、2014年に技術研究組合次世代3D積層造形技術総合開発機構(TRAFAM)が設立され、金属3Dプリンターを含む、3Dプリンターのさまざまなプロジェクトが行われています。
従来の金属加工法と金属3Dプリンターの比較
3次元造形体を作るために一層一層積み上げていく加工法を「Additive Manufacturing(AM)」と呼びます。AMは、従来の金属加工法と比べて以下のような特長が挙げられます。
- メッシュやラティス構造、中空構造体などの複雑形状を製作することができる。
- 構造を最適化し、強度を維持したまま部品の軽量化が可能。
- 複数の部品を一体化造形することで、部品点数を減らし、溶接やロー付け、留め具を無くすことができる。また組立作業の削減や工期短縮にも繋がる。
- 金型や鋳型、冶具が不要で、金型などの保管の必要もない。
- 削り出しに比べて材料の無駄が少ない。
- 3Dデータと金属材料があればすぐに製作できるため、短納期での製造が可能。オンデマンド生産が可能なため在庫を抱える必要がなく、需要に応じて生産量を調整できる。
- CADデータから直接製造できるため、設計変更を伴う試作や開発、カスタマイズ製造にも適する。
- デジタル化により職人技術に頼らない生産が可能。金属3DプリンターはDXを実現するツールの一つと言える。
従来の金属加工法のぞれぞれにメリット、デメリットがあるように、金属3Dプリンターにも以下のような課題があります。
- 造形できるサイズや形状、金属材料に制限がある。(金属3Dプリンターの方式やメーカーの機種により異なる)
- どのような形状でも精度良く造形できるわけではなく、造形に適した形状や配置がある。
- 寸法精度や面粗度に関しては切削加工等の方が優れる。
- 従来工法で製造できるものを量産しても、コストメリットが得られない可能性が高い。装置価格や金属粉末などの材料費は従来工法より高価な傾向がある。
- 通常後処理が必要。金属3Dプリンターの方式やメーカーの機種により異なるが、サポート材(中空部分の土台)の除去、熱処理、ブラスト処理、表面仕上げ加工などが必要になってくる。
金属3Dプリンターの種類(造形方式)
金属3Dプリンターは、その造形方式によっていくつかの種類に分けられます。
まずどんな方式があるのか、その特徴について見ていきましょう。
1.パウダーベッド方式(Powder Bed Fusion:PBF / 粉末床溶融結合法)
パウダーベッド方式は金属3Dプリンターの中で最も主流で、世界中で広く利用されています。金属粉末を均等に敷き詰めたパウダーベッド(粉末床)に、熱源のレーザーまたは電子ビームを選択的にスキャンし、溶融・凝固を繰り返し、一層ずつ積み重ねていき造形します。造形が完了したら、周囲の粉末を取り除き、完成した造形物を取り出します。周囲の粉末は回収され、ふるいにかけた後、造形に再利用します。
パウダーベッド方式は、他の方式に比べ高精度で再現性の高い造形ができ、また高密度で強度が高い部品を造ることができるため、航空宇宙や医療分野などでの実績に優れています。
パウダーベッド方式には、加熱源がレーザーと電子ビームの2つの方式があり、それぞれ特徴があります。次の項で詳しく説明します。
【主なメーカー】
・レーザー:EOS, 3D Systems, Nikon SLM Solutions, Colibrium Additive(旧Concept Laser), 松浦機械製作所, ソディック
・電子ビーム:Colibrium Additive(旧Arcam), 三菱電機, 日本電子
パウダーベッド方式におけるレーザーと電子ビームの比較
先に述べたパウダーベッド方式では金属粉末を溶融して造形しますが、加熱源としてレーザーと電子ビームが使用されています。主に以下のような違いがあります。
レーザーパウダーベッド方式 | 電子ビームパウダーベッド方式 | |
---|---|---|
最大出力 | 一般的なファイバーレーザーでは400W~1kW。レーザー源を複数台搭載する機種も多い。 | 3kW~6kW |
ビーム偏向 | 機械的(ガルバノミラー駆動) | 電磁偏向 |
ビームスキャン速度 | 低速(msecオーダー) | 高速(μsecオーダー) |
入熱効率 | 金属材料やレーザー種により大きく異なる。一般的なファイバーレーザーでは概ね5~40%程度(チタンは65%程度)。 | ほぼ全ての金属材料で80%以上 |
造形雰囲気 | 不活性ガス | 真空 |
予熱機能 | なし または 最大200℃程度 | あり(最大1100℃程度) |
その他 | 金属3Dプリンターでは主流。装置の機種が豊富。装置が比較的コンパクト。 | 真空チャンバーが必要 |
一般的な比較内容です。レーザー方式の仕様は、搭載するレーザーの出力や台数、装置メーカーの機種により大きく異なります。
具体的にレーザー方式、電子ビーム方式のメリット、デメリットを見ていきましょう。
レーザーパウダーベッド方式のメリット
まず、レーザー方式のメリットについて説明します。
レーザービームは集光性が高いため、微細な形状や、複雑な内部構造を持つ部品を高精度で造形できます。造形後の表面は比較的滑らかで、後加工の手間が軽減できるという特長がある他、電子ビーム金属3Dプリンタ―に比べて装置が比較的小型で、設置スペースを取らないというメリットもあります。また、世界中で広く利用されているため、造形実績のある材料や、実用化の事例が多いことも特徴です。
レーザーパウダーベッド方式のデメリット
デメリットとしては、均一な予熱を行うことは難しいため残留応力が蓄積しやすく、金属材料や形状によっては変形やクラックが発生してしまう場合があります。そのため、内部応力を緩和させるために造形後に熱処理が行われることが多いようです。
また電子ビーム源と比べると出力がやや小さく入熱効率が低いため、造形速度が比較的遅く、大きい部品や大量の生産にはどうしても時間がかかります。レーザーを複数台搭載したマルチレーザータイプでは大型部品の造形が可能ですが、完成までに日数を要します。
電子ビームパウダーベッド方式のメリット
次に、電子ビーム3D金属プリンターについて見ていきましょう。
電子ビーム装置は、溶融前にパウダーベッド面全体を電子ビームで高速にスキャンし、短時間で数100℃~1000℃程度に予熱することができます。ホットプロセス(電子ビーム余熱)により残留応力を抑制することができるため、造形物の歪みやクラックを抑えることができます。またレーザー方式に比べてサポート材が少なくて済むこともメリットです。電子ビームはレーザーより高出力で熱エネルギーへの変換効率が高いため、造形速度が速く、大きめの部品の製造や、一度にまとめて量産する場合に強みを発揮します。また、電子ビーム方式は真空環境下で造形を行うため、酸素や水分の影響を抑えることができ、チタン合金などの活性金属の造形に適しています。タングステンやモリブデンなどの高融点金属や純銅のように、ファイバーレーザーでは吸収率の低い材料にも適しています。
電子ビームパウダーベッド方式のデメリット
その一方、電子ビーム金属プリンターにも課題があります。
まず電子ビーム方式は、予熱の際に造形物の周囲の粉末同士が軽く結合されるため、造形後に仮焼結された粉末をブラストで取り除く必要があります。内部流路があったり、内部が複雑な造形物の場合は、仮焼結粉末をブラストで除去することが困難なため、複雑な水管を有する金型などの造形は不得意としています。
使用する金属粉末の粒径はレーザー方式より大きい粉末を使用しているため、微細形状の精度や表面粗さはレーザー方式の方がやや優れています。
また、レーザー装置に比べると装置メーカーは多くはなく、造形実績のある材料もまだ限定的なため、今後の造形材料の広がりを期待したいと思います。
2.DED方式(Directed Energy Deposition / 指向性エネルギー堆積法)
DED(デポジション)方式は、金属粉末や金属ワイヤーを連続的に供給しながら、レーザーまたは電子ビーム、アーク放電のエネルギーで溶融し、堆積していく造形方法です。
他の方式と比べて造形速度が速く、大型の部品を造形できることが大きな特長です。
一方、寸法精度や面粗度は一般的にパウダーベッド方式の方が優れ、造形できる形状にも制限があるため、微細な部品や複雑形状の部品は不得意としています。
ノズルから肉盛りのように堆積していくため、異種金属や部品の上に形状を付加できる他、部品の補修用としても広く利用されています。装置機種により、造形中に供給する金属を切り替えることで異種金属の造形を行うことも可能です。
【主なメーカー】
・レーザー(粉末): DMG森精機, ニデックマシンツール, ニコン, 芝浦機械
・レーザー(ワイヤー):三菱電機, Meltio
・アーク(ワイヤー): WAAM3D
・電子ビーム(ワイヤー): Sciaky, pro-beam
3.FDM方式(Fused Deposition Modeling / 熱溶解積層法)
一般的な樹脂の3Dプリンターと同じ原理です。材料を押し出して造形する方式で、材料押出方式(Material Extrusion: MEX)とも呼ばれます。金属粉末と、バインダー(結合剤)となる熱可塑性樹脂材料を混ぜたフィラメントを、熱で溶かしてノズルから押し出しながら積層します。造形後にバインダーを取り除く脱脂工程を経て、炉で焼結します。焼結時に体積が約20%収縮するため、それを見越したサイズで造形を行う必要があります。材料のロスが少なく金属粉末の取り扱いが容易です。他の方式と比べて、安価で操作が容易なため試作や少量生産に適していますが、密度にやや課題があります。
【主なメーカー】
Stratasys, Nano Dimension(旧 Desktop Metal)
4.バインダージェッティング方式(Binder Jetting)
敷き詰めた金属粉末に、ノズルから選択的に液体の結合剤(バインダー)を噴射しながら一層ずつ固化させます。FDM方式と同様に、造形後にバインダーを脱脂工程で除去して、炉で焼結します。焼結時に体積が約20%収縮します。造形時に高温の熱源を必要とせずサポート材が不要です。パウダーベッド方式と同様に、造形に利用されなかった金属粉末は再利用できます。スループットが高く、量産に向いている可能性を秘めていますが、パウダーベッド方式に比べると密度や強度が低い傾向があり、実用部品への適用が課題となっています。主に微細形状の小型部品の造形を得意としています。
【主なメーカー】
Nano Dimension(旧 Desktop Metal), Markforged (旧 Digital Metal), Hewlett Packard
他にも超音速堆積法(ノズルから金属粉末を高速で吹き付け金属粒子を結合)や液体金属堆積法(インクジェットの金属版で、金属粒子の懸濁液を吹き付け、高温で結合させ堆積)などがあります。
日本電子JAM-5200EBMの特徴と仕様
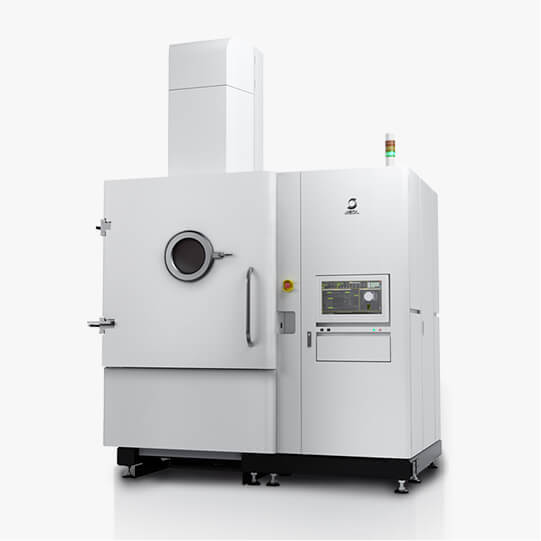
最後に、日本電子が開発した電子ビームパウダーベッド方式の金属3Dプリンター、JAM-5200EBMについてご紹介します。
JAM-5200EBMは、高出力の6kWの電子ビーム源を搭載しており、高い生産効率を実現します。カソードは長寿命で、電子ビーム自動補正機能を有し、粉末飛散防止ユニットが備わっているため、長時間安定した電子ビーム照射により再現性のある生産を行うことができます。
関連製品
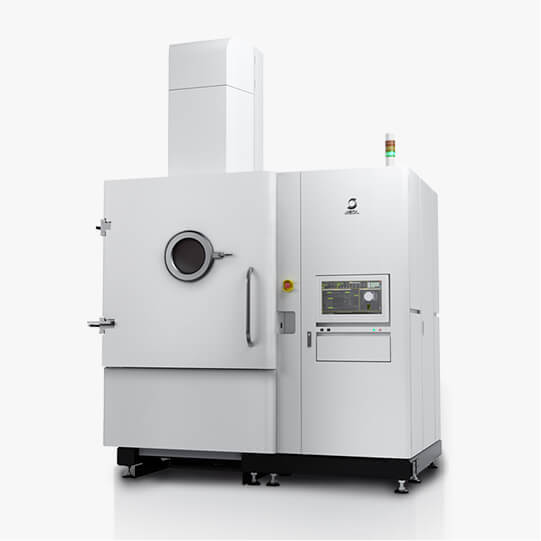
JAM-5200EBM 電子ビーム金属3Dプリンター
当社は電子顕微鏡や半導体製造用電子ビーム描画装置で培った電子ビーム技術を応用して電子ビームパウダーベッドフュージョン(EB-PBF)方式の金属3Dプリンター「JAM-5200EBM」を開発しました。パウダーベッドフュージョン方式は他の金属3Dプリンター方式と比べて、高密度で強度が高く、また高精細で複雑な形状も造形することができます。 JAM-5200EBMは造形中の不活性ガス導入が不要で、長寿命カソードを搭載し、高精度な自動ビーム補正技術により再現性の高い生産が可能となっています。レーザー装置では造形が困難な高融点金属や純銅も造形することができます。
導入事例
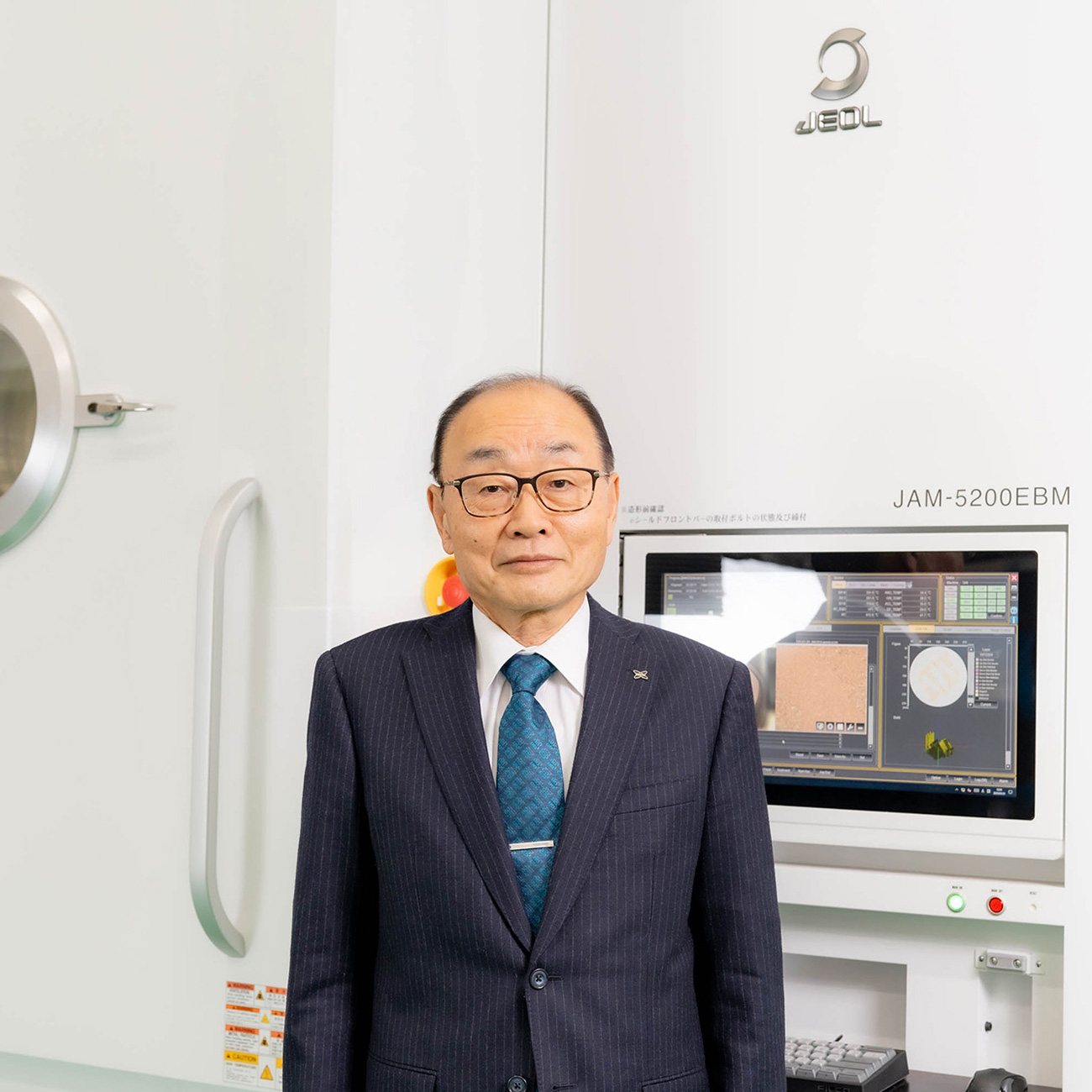
日本電子工業株式会社様~高周波焼入れ技術の進化を支える金属3Dプリンター
日本電子工業株式会社は、高周波焼入れ技術の分野で長年の実績を持ち、金属積層造形技術を採用することでさらなる進化を目指しています。今回のインタビューでは、日本電子工業が金属3Dプリンターを導入した経緯や今後の展望、日本電子に寄せる期待について詳しくお話を伺いました。
開発秘話
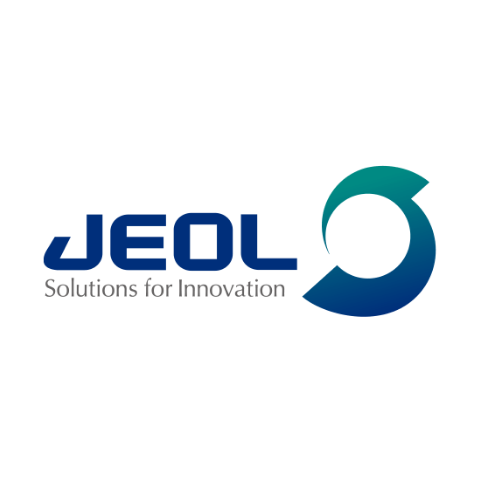
日本電子株式会社
日本電子は、1949年の創業以来、これまで最先端の理科学・計測機器、産業機器そして医用機器の開発に邁進してきました。
今では数多くの製品が世界のいたるところで使用され、真のグローバル企業として高い評価を頂いております。
「世界の科学技術を支えるニッチトップ企業」を目指し、ますます高度化し多様化するお客様のニーズに的確にお応えしていきます。
お問い合わせ
日本電子では、お客様に安心して製品をお使い頂くために、
様々なサポート体制でお客様をバックアップしております。お気軽にお問い合わせください。