JAM-5200EBM開発の軌跡--電子ビーム金属3Dプリンターが目指す未来
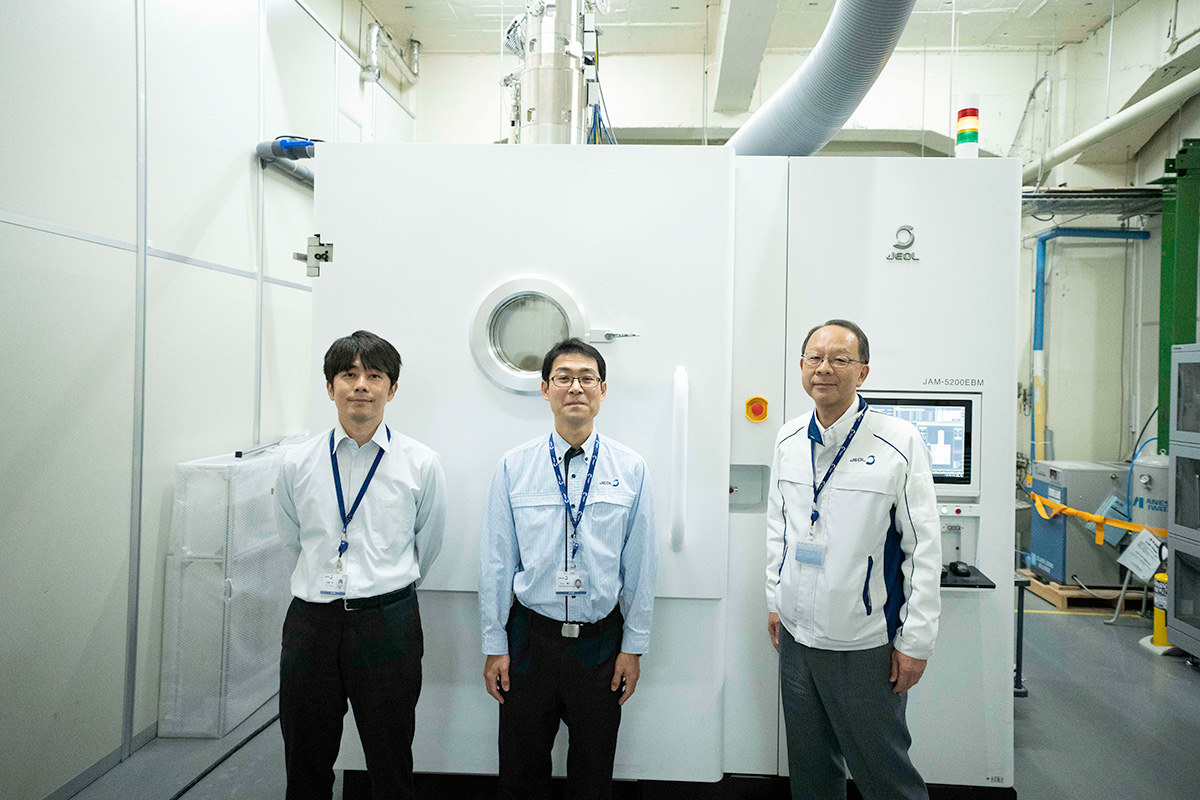
日本電子株式会社は、金属3Dプリンターという新たな分野への挑戦を通じて、ものづくりの未来を切り開こうとしています。その中心にあるのが、電子ビーム技術を駆使した「JAM-5200EBM」。この装置は、タングステンのような高融点金属を加工可能にし、航空・宇宙、医療などの高度産業での活用が期待されています。この記事では、プロジェクト責任者の眞部弘宣氏をはじめとする開発メンバーへのインタビューを通じ、開発の背景、苦労、そして製品に込められた想いや未来への展望を掘り下げてご紹介します。
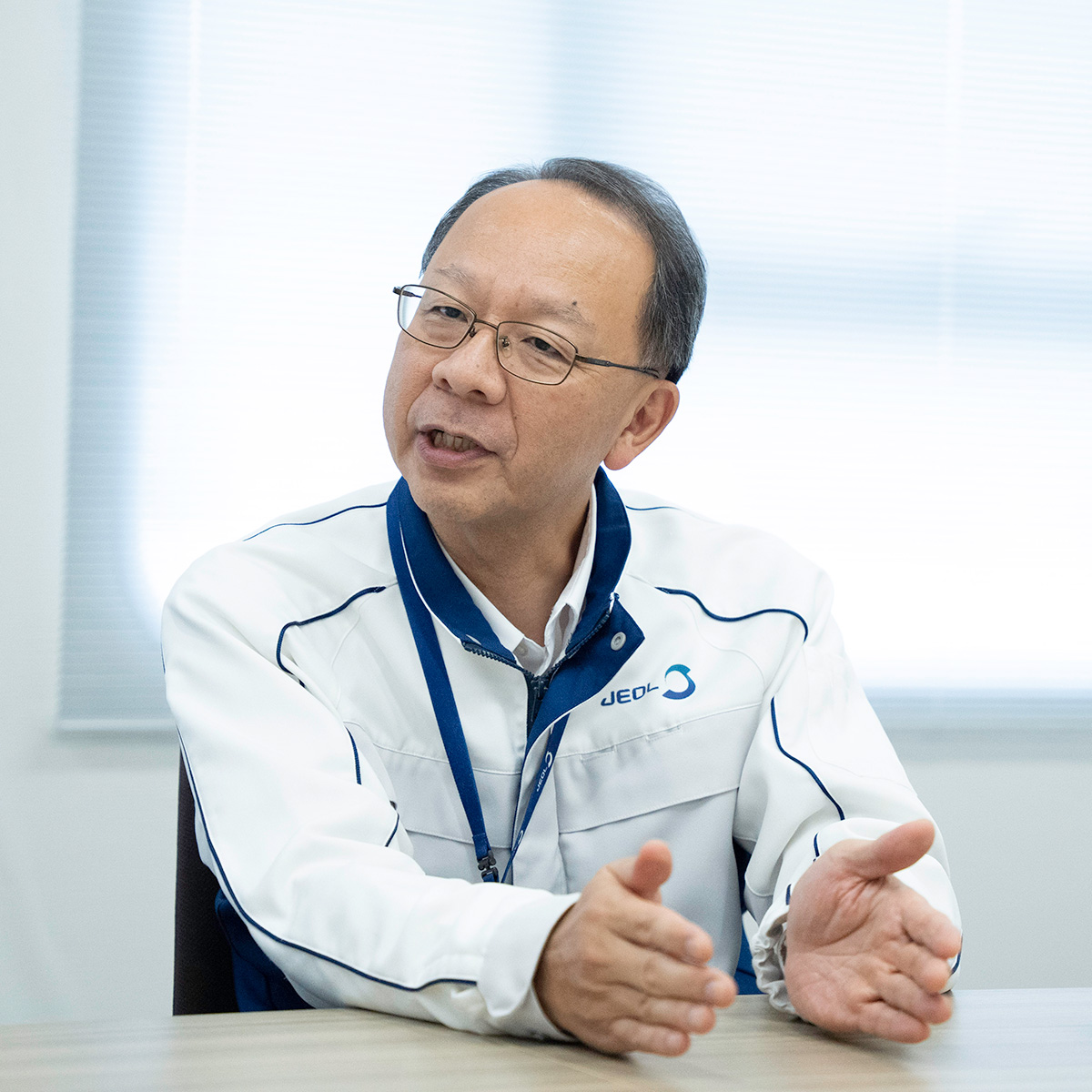
3D積層造形PJ プロジェクト長
眞部 弘宣 さん
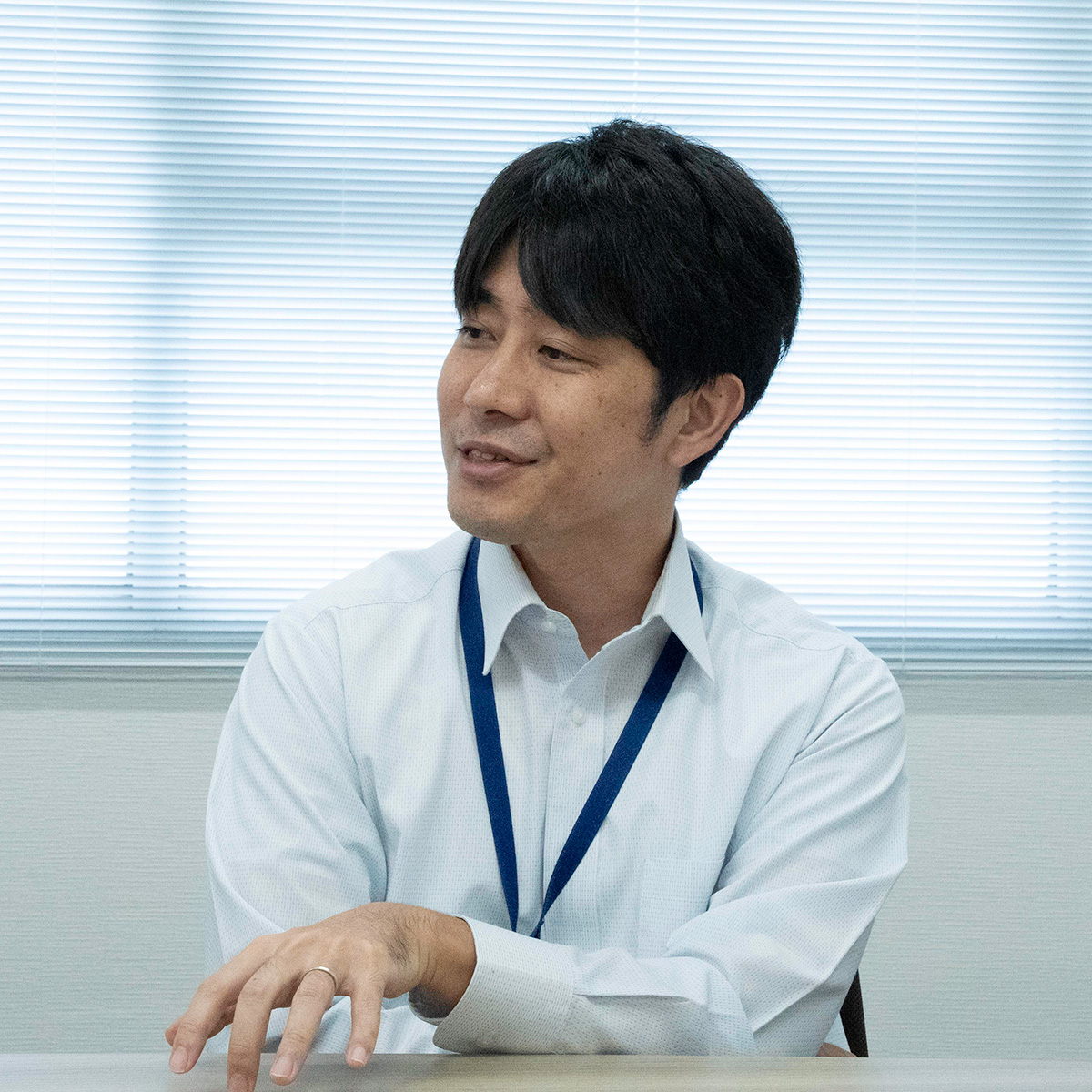
3D積層造形PJ プロジェクト長代理
佐藤 崇 さん
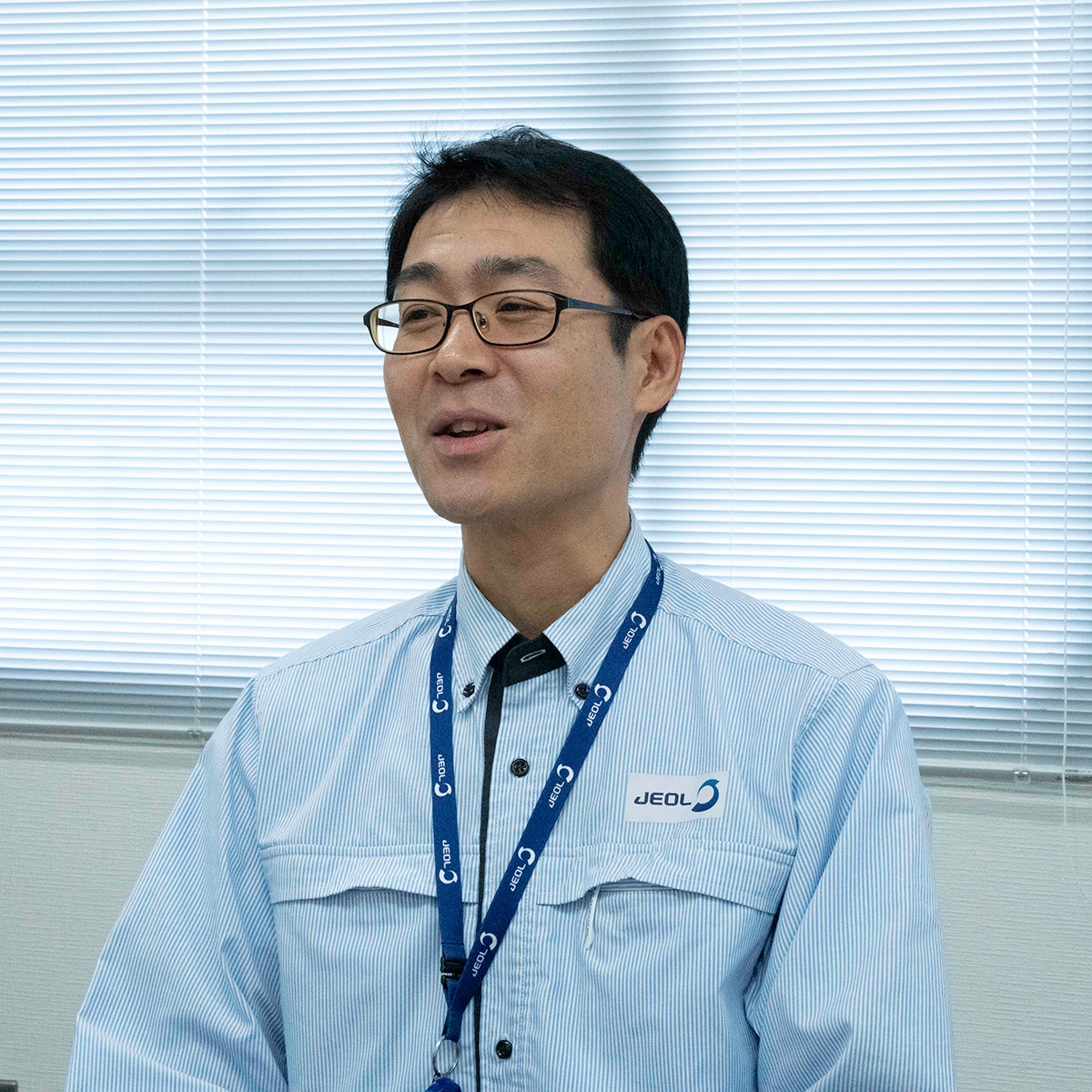
3D積層造形PJ 設計G
山上 暢久 さん
世界に後れをとる日本に危機感を抱いた
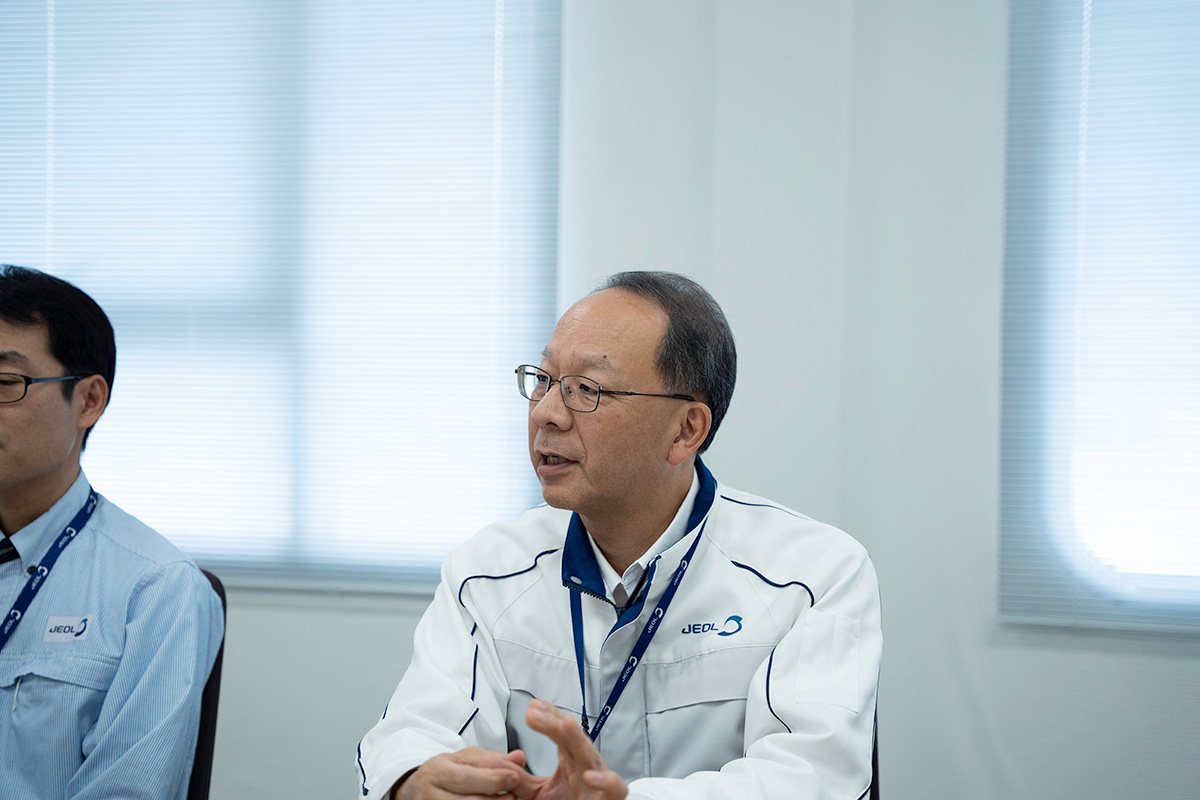
――日本電子が金属3Dプリンターを開発することになった経緯を教えてください。
眞部:2014年、経済産業省が主導する「TRAFAM」というプロジェクトがきっかけでした。当時、日本は金属3Dプリンターの分野で欧米に大きく遅れをとっていました。特に航空や宇宙産業では、3Dプリンターを活用した軽量化や複雑な構造物の製造が進んでおり、日本がこの分野で競争力を失いつつある状況に危機感を持ちました。
――なぜ日本電子が選ばれたのでしょうか。
眞部:日本電子は電子ビーム技術の分野で世界的な実績がありました。また、東北大学の千葉教授をはじめとする研究者から、「金属加工において電子ビーム技術を活用できる企業は日本電子しかない」と高い評価をいただいたことも選定の決め手でした。国としても、日本のものづくりを支える一員としての期待が大きかったと思います。
――このプロジェクトを社内で進める上で、どのような意見がありましたか?
眞部:3Dプリンターは当社の主力事業ではなく、社内では「本当に成功するのか?」という声もありました。ただ、私は電子ビーム技術を活かす新たな可能性をこの分野に見出し、上層部を説得しました。試作機をわずか1年で完成させるという厳しい条件でした。しかし、日本電子の技術者たちの力を信じ、プロジェクトを進めました。
他部署での経験を活かし開発に取り組んだ
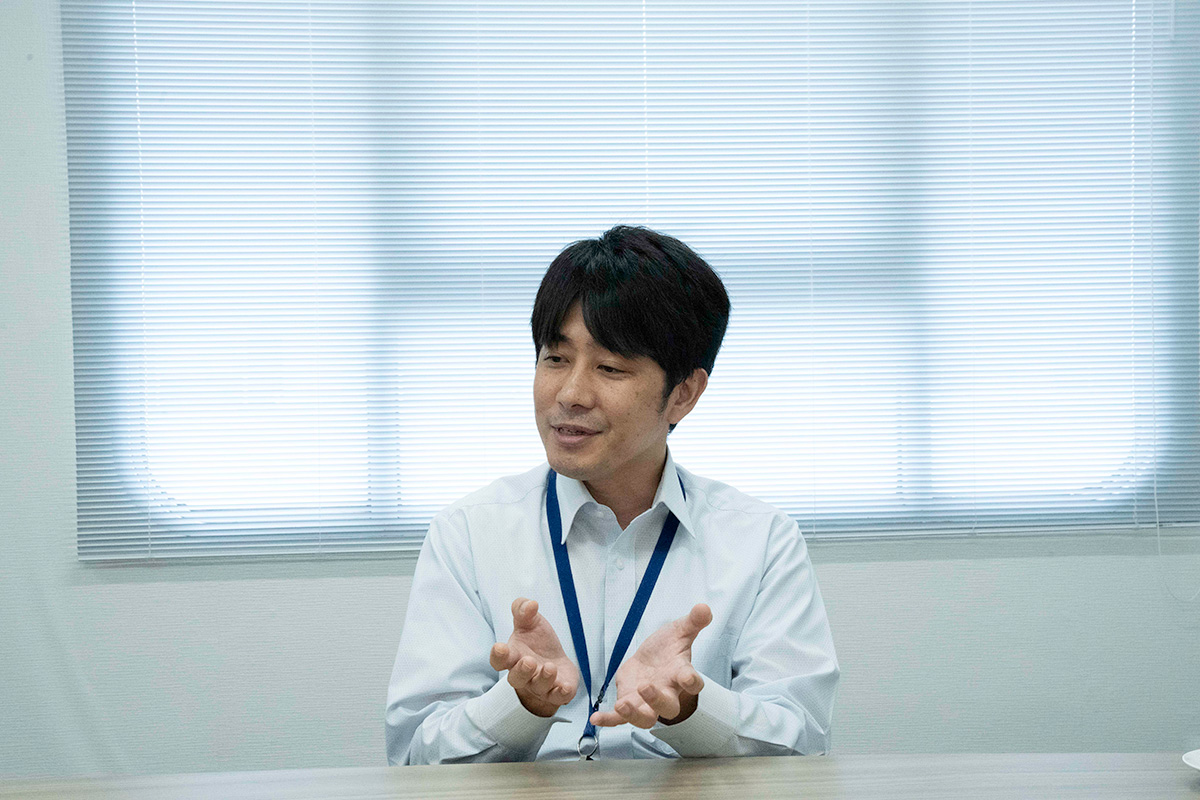
――プロジェクトにおける役割を教えてください。
佐藤:私は技術グループ長として、製品の設計から量産化までを統括しました。具体的には、試作段階から実用化までのプロセスを設計チームと共に策定し、プロトタイプの改善や生産効率の向上に取り組みました。
日本電子に入社してから、半導体分野で電子銃(エレクトロンガン)の開発などを担当していました。その際に培った微細加工技術や電子ビームの特性制御のノウハウが、このプロジェクトでも大いに役立ちました。また、開発中には予期せぬ課題が頻出しましたが、設計者として問題の本質を見極め、迅速に解決策を導き出す役割を担いました。
山上:私は設計グループで電気設計を担当しました。特に装置全体の安全性を確保するための設計や、海外市場で求められる厳しい安全規格に対応するための認証取得に取り組んでいました。それ以前は分析機器の電気設計を担当しており、そこで得た信号処理や回路設計の知識を本プロジェクトで活かすことができたと思っています。
また、JAM-5200EBMのような大型装置では、すべての部品が連動して動作する必要があります。そのため、制御システムの安定化や誤作動を防ぐための設計を徹底的に見直し、最終的には耐久性と信頼性を兼ね備えた装置に仕上げることができました。
眞部:私はプロジェクト全体を統括する立場として、開発の方向性を定めるだけでなく、国プロとしての進捗管理やチームの士気を高める役割を担いました。これまでのキャリアで、イオンビーム装置や電子ビームマスク描画装置など、国内外で評価の高い装置を手がけてきました。これらの経験を通じて、技術的な課題を見通す力やプロジェクト全体を俯瞰する視点を培ってきました。国のプロジェクトであり、厳しい条件が課されていましたが、メンバー全員が持つ専門知識と粘り強さを信じて進めることで無事に目標を達成することができました。
装置の安定性確保や認証取得に苦心
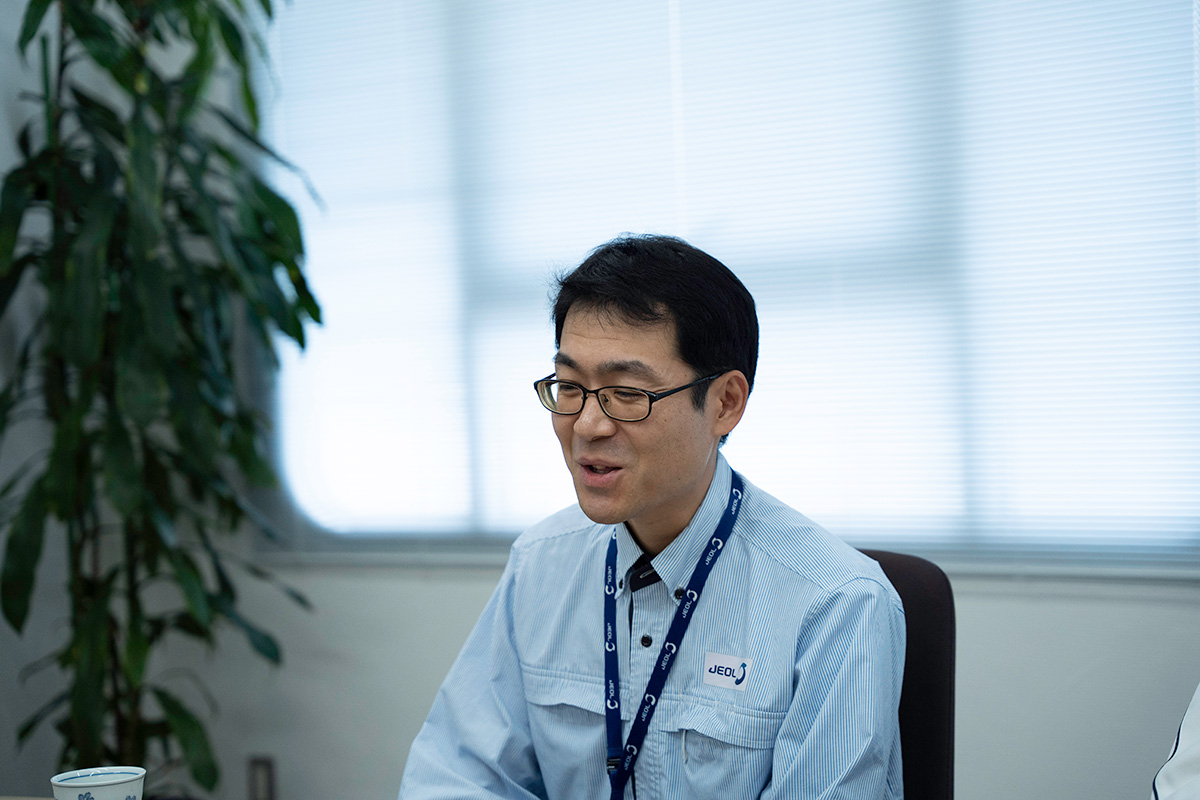
――JAM-5200EBMを開発する際に直面した課題は何ですか?
佐藤:装置の安定性を確保することが大きな課題でした。電子ビームが途中で止まるトラブルや、粉末の敷き詰めが均一でない問題などがあり、試作段階では何度も修正を重ねました。1つの部品を製造するのに数日を要する場合もありますから、その間ずっと人間が見張っている、というわけにはいきません。かといって、見に行ったら途中で止まっていた、というのでは実用化できません。その間の無人運転を実現するためにハードウェアとソフトウェアの改良を繰り返しました。
山上:海外の安全規格や品質認証の取得が苦労した点です。特に航空・宇宙分野では非常に厳しい基準が求められるため、それに対応する設計を行うのは大変でした。安全性を確保しつつ、装置のコストを抑えるバランスを取ることに苦労しました。
眞部:繰り返しになりますが、初年度に試作機を完成させるという条件が非常に厳しかったです。しかし、「できないかもしれない」と思ったことは一度もありませんでした。メンバーを信じて開発を進めていたからです。結果的に、限られた時間と予算の中で試作機を完成させることができたのは、技術者一人ひとりの努力の賜物です。
高融点金属の加工に強み
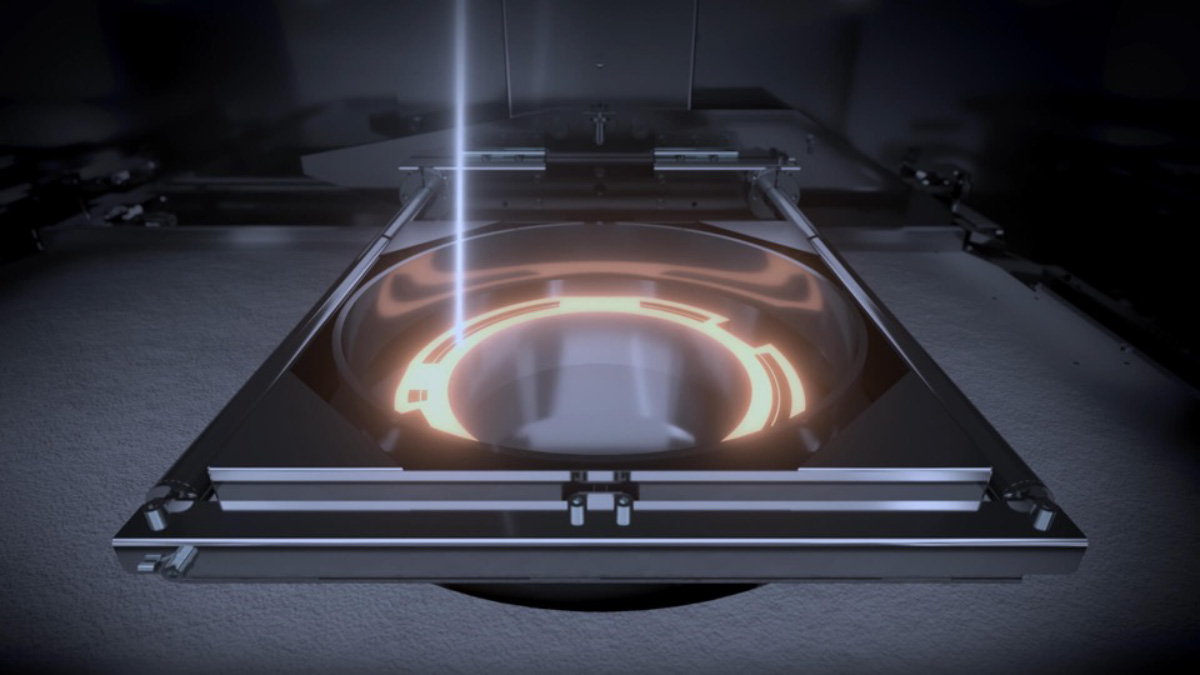
――競合他社製品と比べて、JAM-5200EBMの特長は何ですか?
佐藤:JAM-5200EBMの最大の特長は、1,600度という高温でワークを予熱しながらタングステンやモリブデンなどの高融点金属を加工できる点です。他社製品では対応が難しいこれらの金属も、当社の電子ビーム技術を使えば安定して造形が可能です。
山上:さらに、AMS認証を取得していることも挙げられます。これにより、航空や宇宙産業の厳しい品質基準を満たすことが可能になりました。また、装置の信頼性や耐久性にも優れています。
眞部:JAM-5200EBMは、ただ金属を成形するだけでなく、従来の切削加工では実現できなかった内部構造を作ることができます。削り出しでは内部を空洞にすることができませんが、3Dプリンターであれば可能になるので、パーツの軽量化につながりますし、原材料の無駄が減ることでコスト削減にも貢献できます。この自由度の高さが、3Dプリンター技術の最大の魅力だと思います。
ひらめきを大切に、最後まで諦めない
佐藤:私はエジソンの「1%のひらめきがなければ、99%の努力は無駄になる」という言葉に深く共感しています。この言葉は、単に「努力だけでは足りない」と言いたいわけではなく、成功するためには最初の方向性が極めて重要だということを示していると考えます。例えば、開発の初期段階で設定する仕様や設計の目標が、最終的な成果にどれほど大きな影響を与えるかを痛感する場面が何度もありました。そのため、私は常にチームと議論を重ねながら、その「1%のひらめき」を見つける努力を続けてきました。
山上:私が信条としているのは「失敗を恐れず挑戦する」という姿勢です。技術開発の現場では、一度や二度の失敗で諦めるのではなく、その失敗から何を学ぶかが重要です。JAM-5200EBMの開発でも、試作段階で何度も問題に直面しましたが、そうした状況で「失敗を恐れず、何度でも試す」という信念を貫きました。この考え方は、大学時代に研究していたプラズマ物理の分野でも生きていて、理論だけでなく実験を繰り返す中で本質に近づいていくという姿勢を培いました。
眞部:私は渋沢栄一や稲盛和夫氏の教えに大きな影響を受けました。特に稲盛さんの「最後まで諦めない」という言葉は、プロジェクトを進める上で常に意識していました。例えば、国の補助金で進めるプロジェクトには厳しい進捗管理があり、予算や期限に縛られる中で多くの課題を乗り越えなければなりませんでした。その中で、いかにして困難をチームと一緒に乗り越えるかを考え続けることで、この言葉の重みを実感しました。また、渋沢栄一が語った「誠実であることの大切さ」も私の信念の一つです。技術者として、お客様に信頼される製品を提供するためには、誠実な姿勢が欠かせないと感じています。
日本の競争力向上や後進の育成に尽力したい
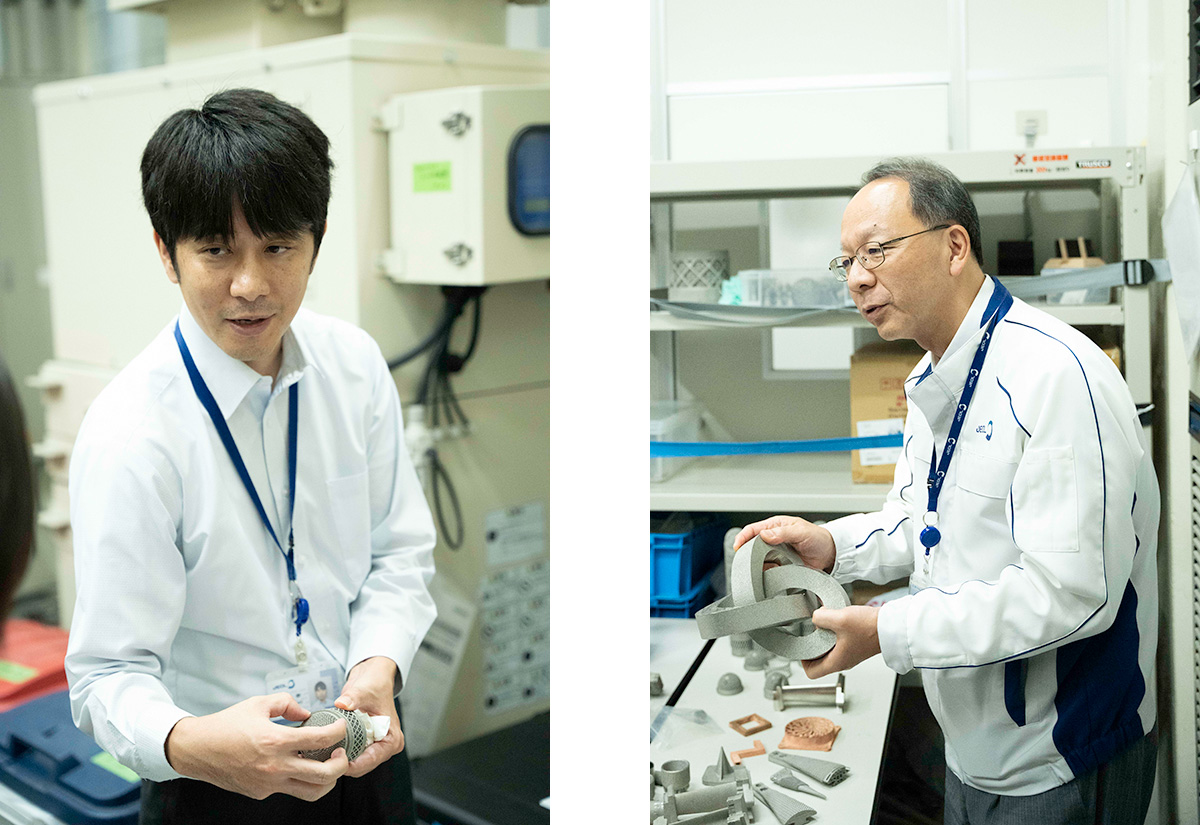
――では最後に、今後実現したいことや意気込みについて教えてください。
眞部:現在はプロジェクトから離れましたが、JAM-5200EBMの技術が金属3Dプリンターの分野で日本の競争力を高めることを信じています。これまでの取り組みで得られたノウハウを基盤として、さらに効率的で多機能な装置を開発し続ける必要があります。また、単に装置を作るだけでなく、顧客がその価値を最大限に活かせるよう、アフターサポートや技術教育にも力を入れていくべきです。
この装置は、航空・宇宙、医療など高度な産業での利用が想定されていますが、私は今後さらに多様な分野に応用されることを期待しています。
佐藤:私の役割は、現場で培った経験や技術を若手に引き継ぎ、次世代機の開発を支えることだと考えています。特に、JAM-5200EBMの量産化や実用化で得た知見は、後輩たちが新しい装置を開発する際に必ず役立つはずです。また、次世代機ではさらなるコスト削減と生産性の向上を追求する必要があります。たとえば、これまでタングステンやモリブデンのような特殊金属に特化していた装置を、より汎用性の高い材料に対応させることで、金属3Dプリンターの市場全体を広げられる可能性があると思います。
山上:安全性と効率性の両立が、次世代機開発の大きな課題です。JAM-5200EBMの開発では、航空・宇宙産業の厳しい基準に対応するための設計や試験を繰り返してきましたが、この経験を活かして、より多様な産業で利用できる装置を目指しています。また、ユーザーフレンドリーな設計を強化し、初めて3Dプリンターを使用する企業でも簡単に操作できるシステムを構築したいです。国内外での規格認証やエネルギー効率の向上にも積極的に取り組み、日本の産業全体の競争力向上にも貢献できればと考えています。