電子ビーム金属3Dプリンターがもたらす材料開発の革命
-数千年に及ぶレガシーからの脱却
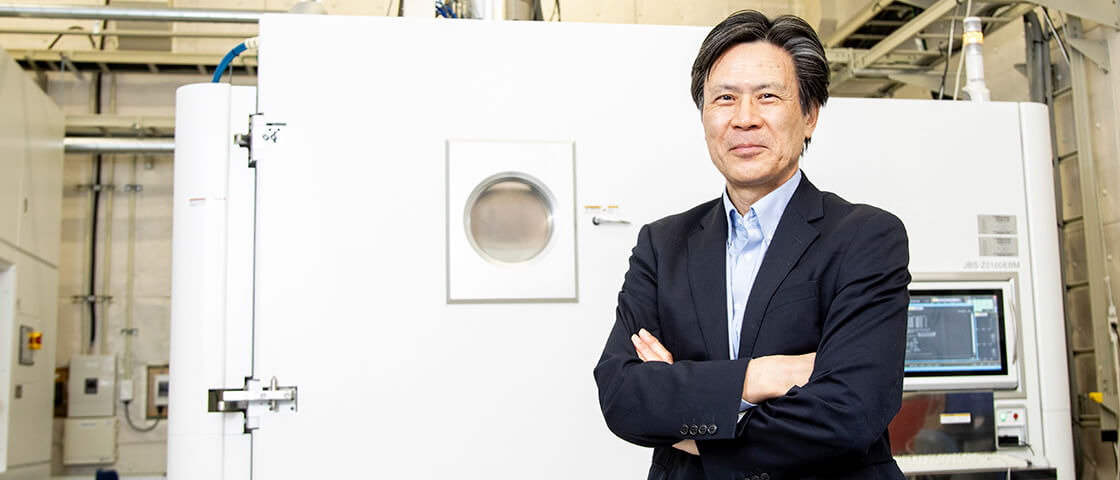
INTERVIEW 10
東北大学金属材料研究所
加工プロセス工学研究部門
千葉 晶彦 教授
電子ビーム金属3Dプリンターがもたらす材料開発の革命
金属部品を3Dプリンターで造形する積層造形技術。強度、信頼度が求められる航空機やロケットの部品に革命をもたらすと期待されている。国内における金属積層造形技術を牽引する東北大学金属材料研究所の千葉晶彦教授に、その可能性を質した。
新たな金属加工プロセスの誕生
人類はこれでまた飛躍的な発展を遂げるかもしれない。といってもAI(人工知能)のことではない。金属の積層造形技術のことだ。
積層造形とはいわゆる3Dプリンターのこと。1980年代後半に誕生し、プラスチックが先行していたが、2000年代には金属を使った積層造形のできる装置も登場した。
「電子顕微鏡で見たら、きれいな単結晶ができている。もはや新たな金属加工プロセスといっていいんじゃないかと強い興味をいだきました」
教授は、初めて電子ビームによる積層造形を目にしたときのことをそう振り返る。もともと3Dプリンターは、試作品を簡単に作ってみせるのに適した加工法とされてきたのだ。だが、結晶がきれいに揃っているということは、十分な強度を持つということでもある。それなら、完成品を前提とした金属加工技術の一つに積層造形を数えてもよいのではないかというのだ。
教授は金属材料開発の第一人者。金属の組織を「微細化」したり、元素の不均一を除去して、強度を高める研究に取り組んできた。人工関節やインプラントに適した金属材料探しも続けている。
「金属の元素と元素をまぜて、溶かして、固めて、熱処理して鍛造する。新たな材料を開発するとはそういうことです」と自らの研究を定義する。
常温では容易に変形しない強度を持ちながら、溶かして型に流し込んだり、削ったり、押し曲げることでさまざまな形に加工できる。しかも木材のように腐ってしまうこともない。金属は理想的な工業原料といえるだろう。有史以来、人は金属を加工することで多くの発明を生み出してきた。武器や神具に始まり、建築資材や自動車の部品、コンピューターや航空機の部品にも金属が多用されている。強度を高める材料開発と加工の効率と精度を高める加工技術の進歩が、新たな発明の礎となり、その発明が、また新たなニーズを生み出して、次の発明を促していった。
現在、市場が金属材料開発に対して期待することの多くは「硬い」ことだ。過酷な使用にも耐えうる強度を持ち、製品に絶対的な信頼性をもたらすことが期待される。ジェットエンジンの燃料噴射ノズルやタービンブレードなどはその最たるものといってもいいだろう。
「硬い材料が欲しいという市場の声は非常に大きい。そして、それに応える硬さを実現することもできます。とはいえ、硬い丸棒やインゴットができたからといって喜ぶことはできません。それを部品に加工できて初めて実用化できる。ところが、ときには硬すぎて削れないということもある。材料開発は、組成だけでなく、その先の加工プロセスも一緒に考えなければいけないのです」
たとえばチタンは、鋼鉄以上の強度を持ち、質量は鋼鉄の約半分、航空宇宙分野では理想的な材料のひとつだ。だが、高温ではさまざまな元素と反応しやすくなるため、鋳造や溶接では特別なプロセスを経る必要がある。酸素や窒素を遮断した環境で溶けたチタンを流し込んだり、それができなければ、倍以上肉厚の部品として型に流し込み、そこから必要な厚さまで削って仕上げていく。当然、製造コストは跳ね上がる。
「チタンではさんざん苦労してきた」教授は、早くから3Dプリンターであれば、造形の手間を軽減できるのではないかと期待してきたという。
期待から確信へ
「電子ビームならできる」
だが、2000年代初頭に初めて目にした3Dプリンターは、まったくの期待外れだった。
「金属の粉末にレーザーを照射しながら形を作っていく手法でした。しかし、できあがった部品を見てみると強度が低すぎて、試作ならいいが、製品に使えるのはまだまだ先だなと思ったものでした」
当時、ヘッドとして用いられていたのは炭酸ガスレーザー。波長が長めなので、アルミや銅、チタンなど「色もの」では表面で反射してしまい溶融不足が起こっていた。高温加工時に酸素などと反応することも劣化につながっていると予想された。
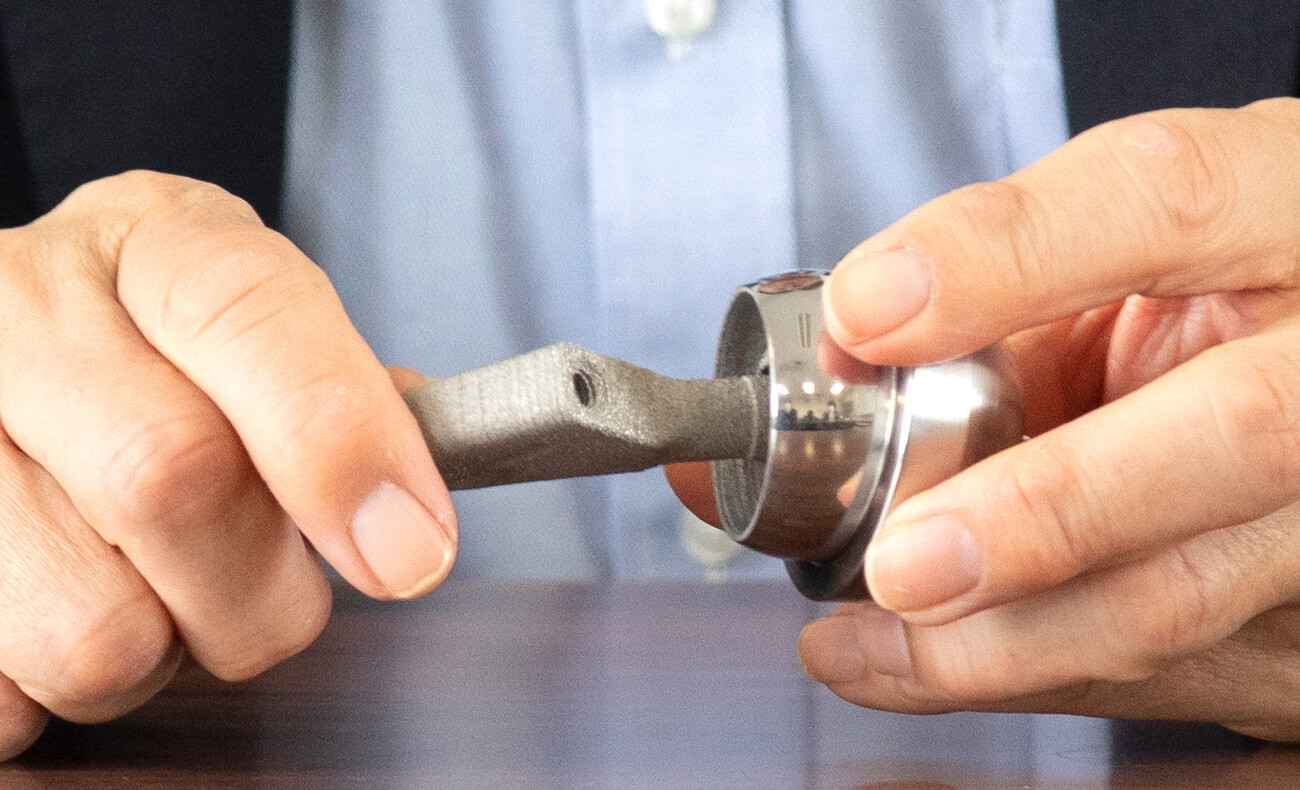
造形された人工関節
それから数年後、学会出席時に同席していたある企業から紹介されたのが、電子ビームを使った積層造形だった。「電子ビーム」という単語に教授は鋭く反応した。
「電子ビームは溶接や電子顕微鏡に使われる技術。いずれにしても真空環境が必須です。真空であれば酸素や窒素の影響を受けずに加工ができるので、材料がチタンであれ何であれ、関係なくなるのではと考えたのです」
そこで見たのが冒頭で紹介した電子ビーム式の積層造形だ。訪れたスウェーデンのヨーテボリの工場で見た人工関節は、十分な強度があり、しかも生体骨との癒合を促すのに適したミクロン単位の多孔質加工も施されていた。
「人工関節として理想的な組成、強度、表面加工が、鋳型を用いることなくできる。何より、一人ひとりの患者さんの体に合わせてオーダーメード加工できるというのは革新的でした」
その可能性に惚れ込んだ教授は装置を購入し、「まったく新しい金属加工プロセス」によってどのような材料的な特徴がもたらされるか、徹底的な研究を重ねた。その結果、見えてきたのは従来の加工法に劣るどころか、これまでのどんな加工法でも及ばない優位点だった。それが「材質分布の均一さ」だ。
通常、合金を作るときは、材料となる金属を溶かし合わせた後、いったん冷やしてインゴットにする。この冷える間に、重い元素は下に沈み、軽い元素は上に集まる。こうすると、インゴット中に材質の不均一(=偏析)が生じてしまう。材質が不均一であれば、強度などの特性も不均一となる。小さなインゴットであればそれほど問題にならなくても、一辺が数メートルに及ぶような大きなインゴットでは、凝固に時間がかかるため、偏析も無視できないレベルに及ぶ。だが、粉末をその場で溶かして造形する積層造形では、この不均一が生じ得ないのだ。
また、鋳造で金型に流し込むとき、金型に近いところは急速に冷やされるが、遠いところはゆっくりと固まる。そうすると中心部に空洞ができることがある。
「本来であれば致命的な欠陥ですが、避けることができないためにどうにか折り合いをつけてきた歴史がある。とはいえ、ジェットエンジンのタービンなど、安全性が極めて重要な部品では許されることではない。積層造形ならこれも避けられるのです」
強度試験では型に入れて鋳造した後、叩いたりさらに熱を加えて強度を増す鍛造に比べても、高い強度が得られることが明らかになった。課題は、製造にかかる時間とコストだが、「科学技術はいつもよい方へと進化を続けてきた。いつか課題が解決される」と期待を寄せる。
電子ビームのノウハウ持つJEOLと共同開発
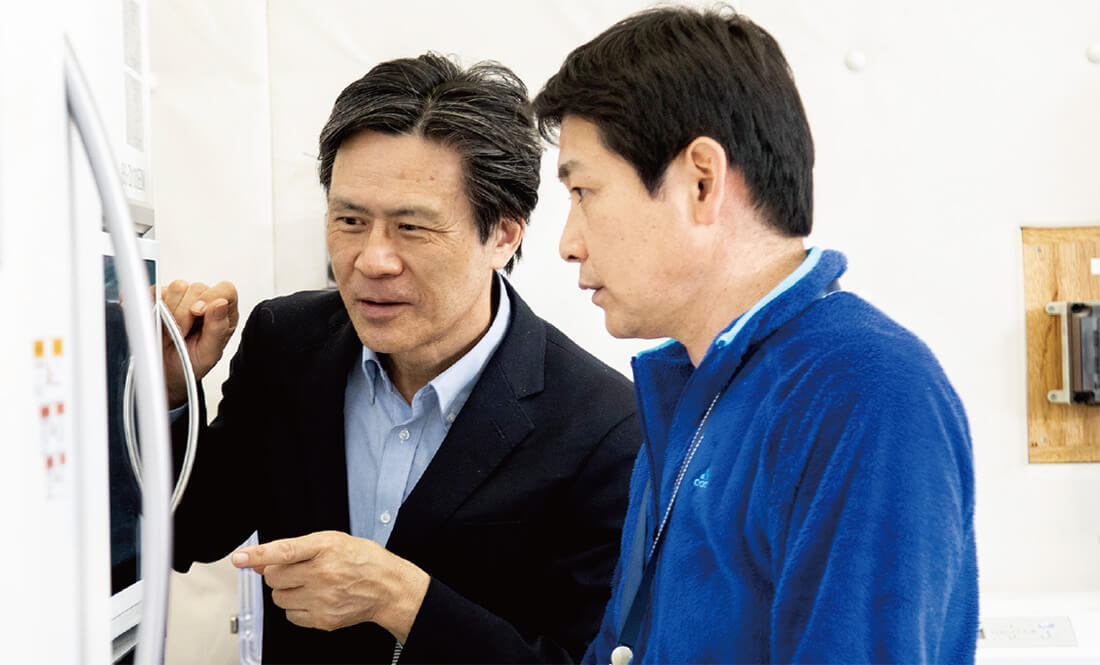
右は、柳原圭司 学術研究員
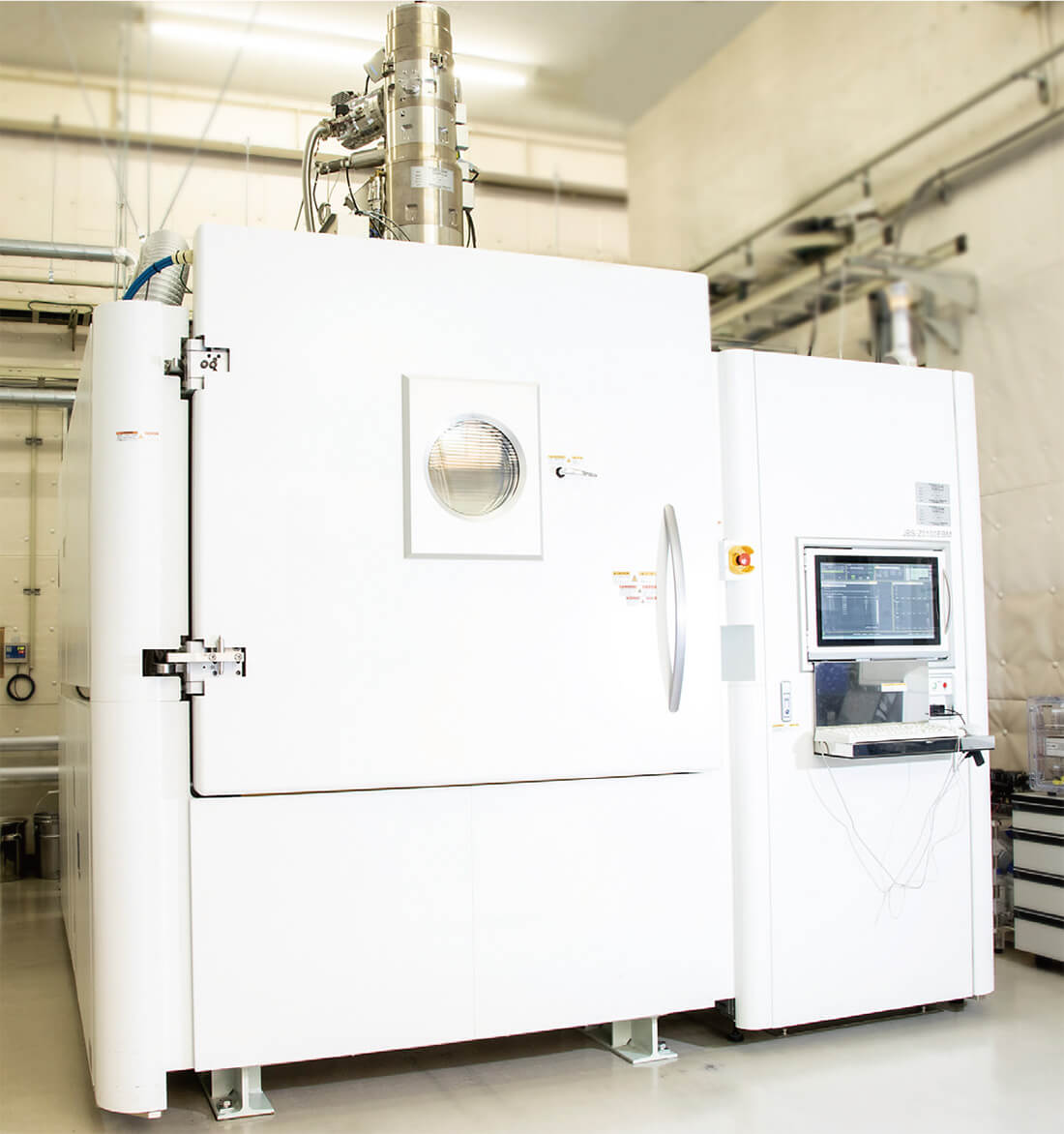
TRAFAM事業の電子ビーム金属3Dプリンター試作機
積層造形の研究を続ける教授が、もうひとつ力を入れてきたのが、国産の電子ビーム金属3Dプリンターの開発だ。パートナーに選んだのは電子顕微鏡のメーカーであるJEOL。
「電子顕微鏡はナノメートル単位で電子ビームを制御する。その技術を用いれば、世界一の3Dプリンターを開発できてもおかしくない。ぜひ一緒につくりましょうと声をかけさせてもらいました」
こうした経緯から2014年からスタートした経済産業省の3Dプリンター開発プロジェクト「TRAFAM*」にJEOLも参画。2018年までのプロジェクトでは製品の精度を従来の約5倍、速度を10倍、造形可能範囲を約3倍の大きさに広げることを目標としていたが、これらをほぼ達成。現在、千葉教授のもとで試作機の検証が続けられており、間もなく製品化の予定だ(2021年3月の取材日時点)。
「金属加工で型を作って流し込む鋳造、叩いたり熱を加える鍛造の手法は、もう数千年も続けられてきたレガシーです。人類は非常な才能を発揮して、この技術を高めてきましたが、大量のエネルギーを消費し、金型をつくるのに、小さいものでも数百万円がかかるうえ、冷えて小さくなる分や材質分布が偏る分を見込んで製造する必要があるなど、まさにアナログ技術の集合体でした。それが積層造形では、造形時に金属合金の微細組織制御すら行えるようになる。材料開発プロセスと製造加工プロセスが一体となって可視化できるようになれば、材料開発は新時代に入るといってもいい。1日でも早く社会実装に結びつけたい」と意気込む。
数千年に及ぶレガシーからの脱却が迫っている。
技術研究組合次世代3D 積層造形技術総合開発機構
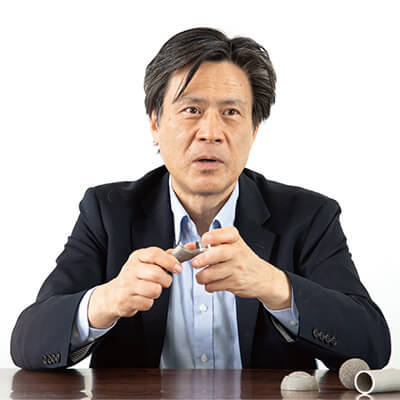
千葉 晶彦(ちば あきひこ)
東北大学金属材料研究所加工プロセス工学研究部門教授
1982年 東北大学工学部金属材料工学科卒業。
1985年日立製作所日立研究所に勤務。
1992年岩手大学工学部助教授、2002年岩手大学教授を経て、2006年より現職。
専門はナノテク・材料 / 材料加工、組織制御 / 加工プロセス工学。
掲載:2021年5月